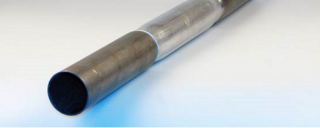
Um funktions- und/oder gewichtsoptimierte Halbzeuge (tailored tubes) für die Innenhochdruck-Umformung (IHU) bereitzustellen, sollen Stahlrohre an beiden Enden mit Aluminiumrohren verbunden werden. Die Fügestelle muss im anschließenden IHU-Prozess bereits beim Schließen der Werkzeughälften signifikante Deformationen des Querschnittes ertragen und darf bei der anschließenden Beaufschlagung mit Innendruck nicht undicht werden. Um diesen Anforderungen gerecht zu werden, wurde die Verbindung stoffschlüssig durch Magnetimpulsschweißen realisiert.
mehr Info