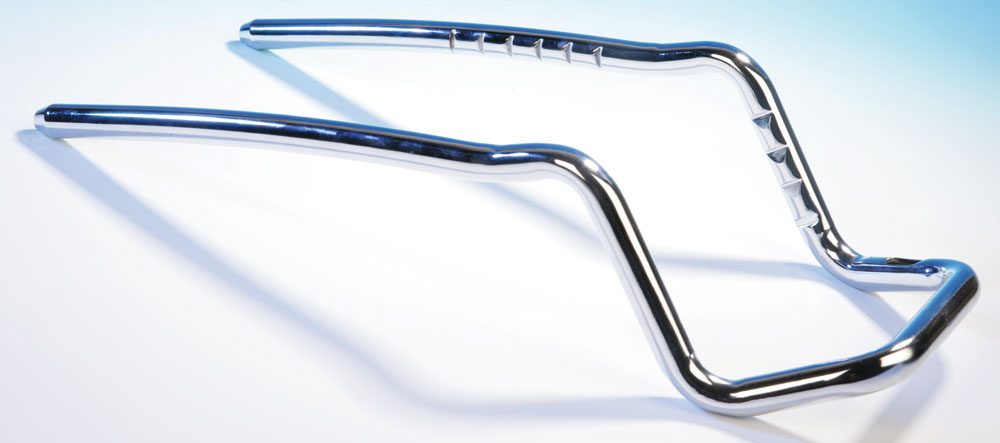
Eine gefährliche Situation, eine Vollbremsung, schlimmstenfalls ein Crash. Abrupt kommt das Auto zum Stehen. Die Köpfe von Fahrer und Beifahrer schnellen erst nach vorn und sofort wieder nach hinten. Dass sich die Halswirbel der Autoinsassen nicht gefährlich weit nach hinten überdehnen, verhindern die Kopfstützen.
Auch diese seit Jahrzehnten etablierten Sicherheitselemente müssen heute maximal wirtschaftlich und ressourceneffizient gefertigt werden, und zwar in allen ihren Teilen. Zu diesen gehört auch der metallene Bügel, auf dem das Polster der Kopfstütze sitzt. Oft ist dort noch ein crashaktives System integriert, das die Kopfstütze in eine für den Schutz des Insassen optimale Position bringt.
Spezialisten des Fraunhofer IWU haben gemeinsam mit einem Industriepartner ein Herstellungsverfahren für Kopfstützenbügel entwickelt, das Leichtbau und höchste Sicherheitsstandards miteinander verbindet. Bei einem konventionellen Herstellungsprozess werden die Kerben des Kopfstützbügels gegen einen Innendorn geprägt. Dabei ist die Realisierung der notwendigen Bauteilqualität und einer ausreichenden Restwanddicke des Rohres eine große Herausforderung. Bei dem von den Fraunhofer-Forschern entwickelten Verfahren wird in ein dünnwandiges Metallrohr durch Innenhochdruck in seine endgültige Form gebracht. Dabei werden im Umformprozess auch die notwendigen Löcher für die Kabelzuführung in die Kopfstütze eingebracht und die Rohrenden umgeformt.
Mit diesem Verfahren, dem Innenhochdruck-Umformen, wird ein Hohlprofil hergestellt, das gleichzeitig ausreichenden Stauraum zur Unterbringung und Aktivierung eines crashaktiven Systems bietet. Darüber hinaus lassen sich Rasterkerben ausformen, die tiefer als die Rohrwanddicke sind.
Der Kopfstützenbügel ist 60 Prozent leichter als herkömmliche Bügel und verfügt über bessere Crasheigenschaften.