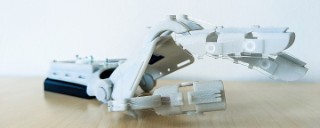
Nach Sehnenverletzungen oder einem Schlaganfall kann die Beweglichkeit der Hände stark eingeschränkt sein. In der Therapie kommen zunehmend Exoskelette zum Einsatz, die wie ein zweites Skelett über der Hand angebracht werden. Sie ermöglichen eine gezielte, langsame Bewegung von Handgelenk und Fingern. Für einen erfolgreichen Therapieverlauf ist es entscheidend, dass das Exoskelett individuell auf die Hand des Patienten abgestimmt ist und zentrale Anforderungen wie geringes Gewicht und kompakte Bauweise erfüllt.
mehr Info