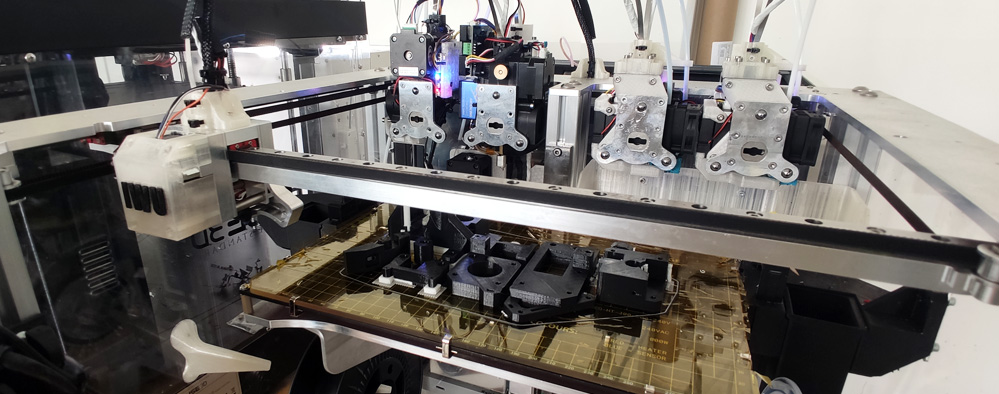
Toolchanger
Wir erleben immer häufiger, dass globale Liefer- und Produktionsketten an ihre Grenzen kommen können. Verteilte Produktionsstätten, lange Zulieferwege und Ressourcenknappheit beeinflussen zunehmend die Versorgungssicherheit. Für eine bedarfsgerechte, lokale Fertigung bieten sich besonders die additiven Fertigungsprozesse an, da es möglich ist, verschiedenste Produkte innerhalb einer Maschine herzustellen. Dabei ist die gängigste Technologie das Fused-Filament-Fabrication-Verfahren, das in vielen Unternehmen und auch Haushalten bereits Einzug gefunden hat. Dieses Verfahren eignet sich besonders gut, um eine Vielzahl von anderen Materialien einzubringen.
Das Fraunhofer IWU beschäftigt sich mit der Erweiterung des 3D-Drucks unter dem Ziel, verschiedenste End-Use-Produkte innerhalb einer Maschine zu fertigen. In der ausgestellten Versuchsanlage können bereits verschiedenste Funktionalitäten umgesetzt werden. Es können unterschiedliche Materialien bedruckt werden, dazu zählen andere Polymerbauteile, Folien, Textilien und Furniere. Durch das Wechselsystem des Prototyps können im Druckprozess vier verschiedene Werkzeugköpfe genutzt werden. Zu diesen Werkzeugköpfen gehören Strukturdruckköpfe, die technische Polymere mit bis zu 500°C verarbeiten können, Pick-and-Place-Köpfe, die Bauteile, elektronische Elemente oder Kontakte automatisiert einsetzen können, und Drahtintegrationsköpfe, die verschiedenste Draht oder Fasermaterialien während des Druckprozesses in das Bauteil einbringen und in gewünschten Bereichen mit Polymer ummanteln.
Mit diesen Kapazitäten können komplexe Strukturen gedruckt werden. So erlaubt der Aufdruck auf Textilien unter Vorspannung dieser die schnelle Fertigung von 3D-Elementen mit textiler Oberfläche. Durch Folienimplemente können gasdichte Körper umgesetzt werden, die sich pneumatisch bewegen lassen. Da mittels der Drahtintegration verschiedene Materialien eingebracht werden können eröffnet sich hier ein komplettes Feld neuer Anwendungen. Bauteile können durch Drahtaufdrucke gerichtet verstärkt werden. Es müssen keine Kabelführungen mehr vorgesehen werden, da diese auch einfach in die Außenhülle eingedruckt werden können. Durch eine automatisierte Kontaktierung müssen folgende Elemente nur in die vorgesehenen Anschlüsse gesteckt werden. So können sowohl Signal- als auch Leistungsleitungen strukturell eingebunden und somit geschützt werden. Diese Drähte können auch genutzt werden, um Sensoren in das Produkt zu integrieren. Es können kapazitive Sensoren in die Oberfläche gedruckt werden, um Interaktionen zu registrieren, oder es werden mittels Formgedächtnisdrähten Belastungssensoren in Strukturbauteile integriert. Diese Sensoren können im Bauteil optimal zur erwarteten Belastung positioniert werden, ohne dabei die Struktur zu schwächen.
Ein weiteres Anwendungsfeld eröffnet die Einbettung von Heizdrähten. Diese ermöglichen es, die verwendeten Thermoplaste im Bereich der Glasübergangstemperatur zu nutzen. In dieser Zone kommt es zu einem Aufweichen, sodass die Polymere sich gummiartig verhalten, jedoch nicht fließen. In diesem Zustand kann der Werkstoff weit über die eigentlichen Streckgrenzen hinaus umgeformt werden. Ein Bauteil kann also in einem Zustand gefertigt, durch die integrierten Drähte lokal erwärmt und in eine bestimmte neue Form gebracht werden und hält nach dem Abkühlen diesen neuen Zustand auch ein. Durch die Heizdrähte kann ein solcher Umformprozess sehr klein aufgelöst und immer wieder vorgenommen werden.
Mit dieser Technologie können bisherige Produkte nicht nur auf einer Maschine gefertigt, sondern können auch neu gedacht werden. Individualisierungsprozesse können auch noch nach dem Fertigungsprozess erfolgen. So können End-Use-Produkte lokal, als one-fits-all-Variante, ohne Anpassungsaufwände produziert werden.