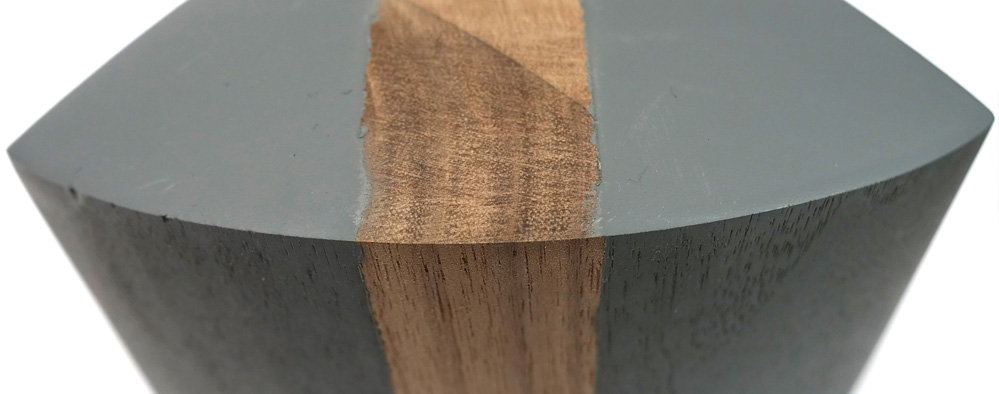
In the future, programming will be child's play. Thanks to SmartGesture, all that is needed to teach the robot the desired sequence of motions is to indicate the points of the motion path with a finger (finger tracking) and specify them with a simple voice command. The robot can immediately follow these motion paths and thus demonstrate that it can implement the desired movements exactly. Programming by finger tracking and voice control can even be done remotely, i.e., regardless of location. Once the robot's entire movement path has been defined, the system has also already defined the safety zone: If a human gets too close, it slows down its movements or brakes to a standstill. For many work tasks, such as painting or polishing, the teaching accuracy of around 0.5 cm, which can be achieved without additional aids, is sufficient. A fingertip attachment can significantly increase precision again if required.
Both cobots and conventional industrial robots can be used for multimodal human-robot interaction. Last but not least, the linking of intelligent path planning and safety zoning in real time enables many application scenarios. The lack of additional devices also keeps the effort low. Only a vision sensor system with RGB-D camera for capturing finger and hand movements and a speech recognition board for voice recognition are required. This opens the perspective for broad application possibilities. The goal is to make robotics even more economical and thus also interesting for smaller industrial manufacturing or handicraft - up to a production rate of 1.
Especially in combination with an intelligent tool that is independent of the robot path, fascinating application possibilities arise. At Automatica, the IWU robotics team will demonstrate how, for example, the cover of a piano keyboard, which is demanding in terms of geometry and surface finish, can be painted quickly and to a high quality with robot assistance. Without any user intervention, the RobFrame software and a digital twin in a virtual commissioning environment optimize and validate the robot path to avoid collisions with the part to be painted or other objects or people. The Dynarisk and SafeZone software packages additionally guarantee maximum safety while minimizing space requirements. An AI solution helps to take into account influencing variables such as the exact nature of the wood surface (grain, roughness), paint properties and light reflections of the wet paint (optical monitoring of the result) in terms of an optimum painting result. This is made possible by decoupling the robot path from the tool behaviour, which, equipped with its own sensor technology, can, for example, finely adjust the amount of paint applied at any position.
The XEIDANA® module performs the final inspection of the painted surface as part of a 100% inspection and, as an AI-based, adaptive tool, also detects unknown defects. Robotics can thus also take on demanding tasks in smaller companies and handicraft environments - and prove its cost-effectiveness.