Energy Balance of Temperature Management in Passenger Compartments, Drive Systems, and Batteries in Trains: A Closer Look is Worth It
The drive system of a rail vehicle is the largest energy consumer in operation, followed by the systems for temperature management of the passenger compartment and the drive system—regardless of the type of train propulsion. Batteries or fuel cells must be maintained at an optimal operating temperature in electrically powered trains without energy supply via overhead lines or third rails. Many rail operators are considering such trains for the nearly 40 percent of non-electrified tracks in Germany. The overall energy consumption in these trains significantly impacts range and potential operating times.
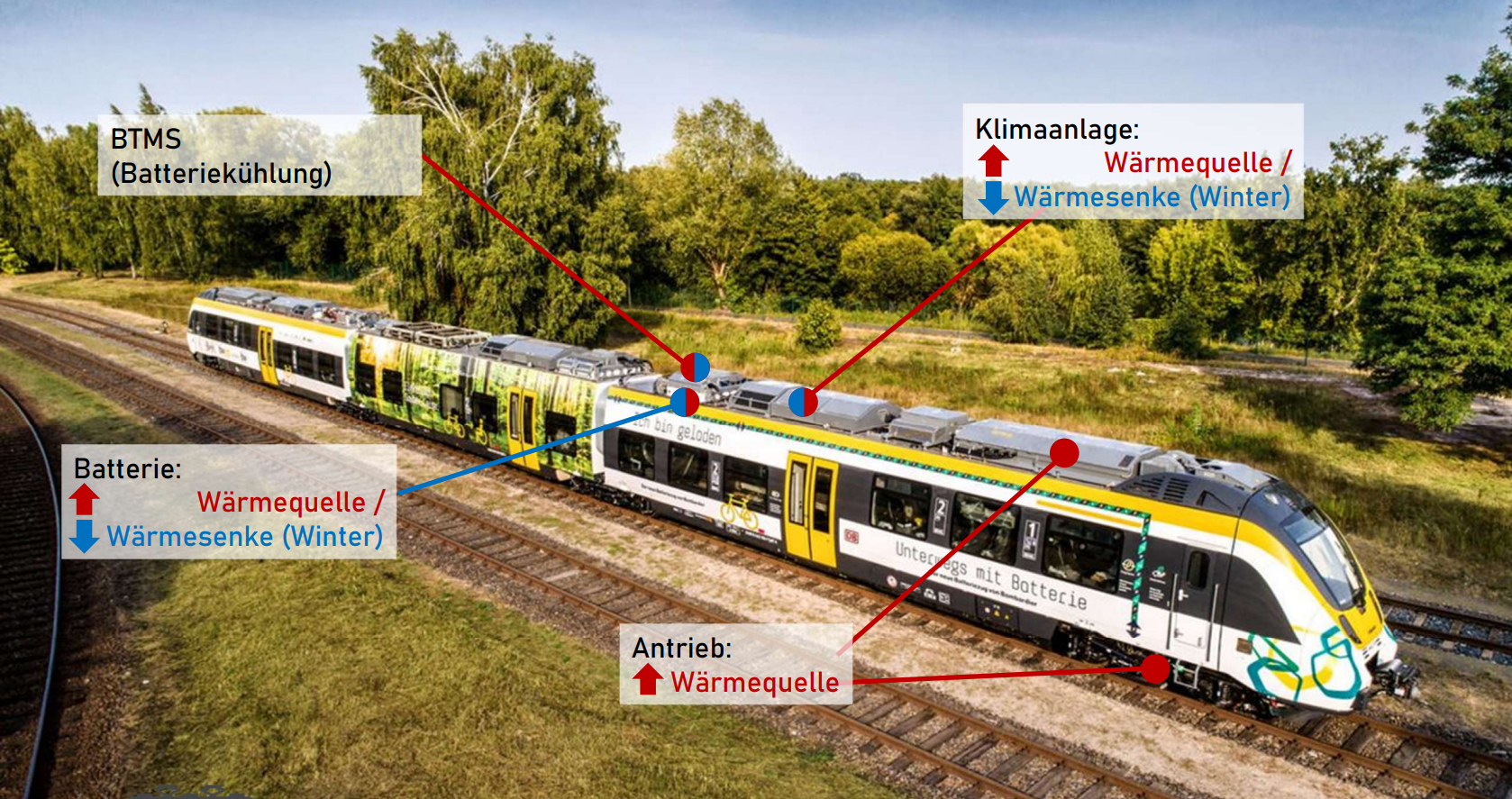
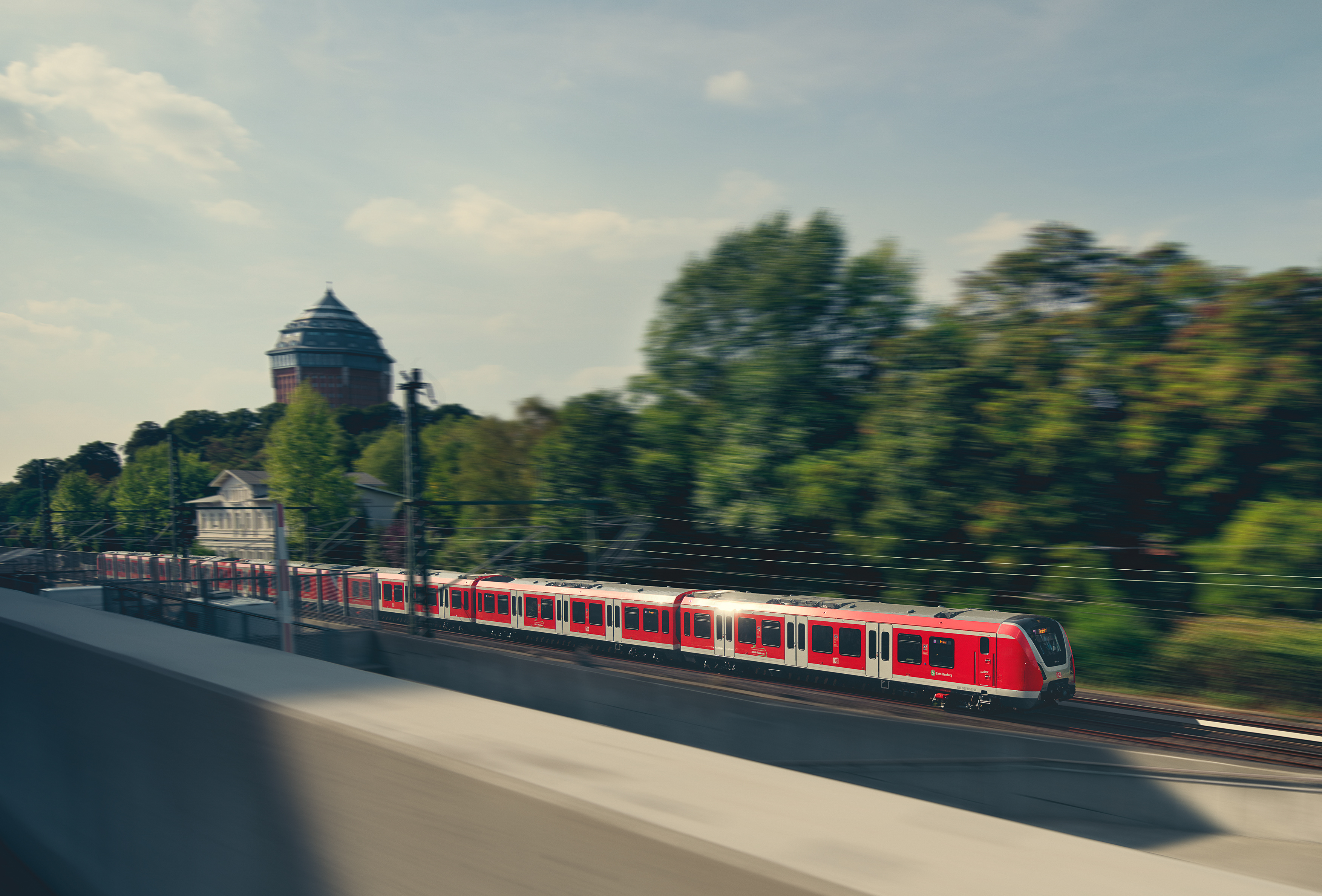
The most suitable strategy for temperature management of the drive system, interior, and any onboard energy storage depends on the drive concept, climate, and operating conditions. The master thesis of Marcos Escamilla Sánchez on the potential of integrated thermal management, which received the Excellent Thesis 2024 award at Fraunhofer IWU, concludes that the DB class 490, used in the S-Bahn (suburban train) operation of Hamburg, has such an efficient thermal management system, thanks to its heat pump and waste heat recovery from traction and auxiliary operations, that continuous development appears most reasonable. This model is a purely electric train without an additional battery. The system's efficiency (Coefficient of Performance) is high throughout the year thanks to the energy-efficient air conditioning and heating.
Sánchez currently works as a systems engineer at the rail vehicle manufacturer Alstom. Together with the climate technology specialist and equipment provider for battery-powered commercial vehicles, Wölfle GmbH, he investigated under which operating conditions an integrated thermal management system could offer efficiency advantages. The idea is to design a total system that connects the drive system and, where present, the batteries and power electronics in a water circuit coupled with a heat pump or chilled water air conditioning system. Such an approach should cover all temperature scenarios: the passenger compartment and battery need to be heated in winter and cooled in summer; while the waste heat from the drive can be utilized in winter, it must be dissipated from the system in summer. The result: a chilled water air conditioning system provides little efficiency gain on average in Hamburg; however, it could demonstrate its advantages in icy regions—where heating is often required throughout the year, whereas cooling is relatively rare. Operators will see the best Coefficient of Performance in a vehicle operation characterized by frequent acceleration and braking, short distances, and frequent stops, which aligns particularly well with the operating profiles of S-Bahn and U-Bahn (subway) systems. An integrated thermal management system could also save weight and require fewer HVAC (Heating, Ventilation, Air Conditioning) components.
Sánchez is confident that the impact of an integrated thermal management system on the energy balance and usability of battery-electric train systems or trains with hydrogen fuel cell propulsion would be substantial, as in such systems, the energy storage requires nearly constant cooling or heating.