New Research Center at Fraunhofer IWU | Trade Fair Premiere at Formnext 2024
Three High-Performance Machines, One SEAM Team: Granulate-Based 3D Printing Revolutionizes Facade Construction
At the new SEAM Research Center, researchers aim to unlock the potential of Screw Extrusion Additive Manufacturing (SEAM) even further. Its centerpiece is Epic3D, a newly developed portal printer that enables the production of large-format plastic components. The continuous deposition process and stiffening structures ensure durable parts, making the technology ideal for producing custom-designed facade elements and other weather-resistant products for the construction industry.
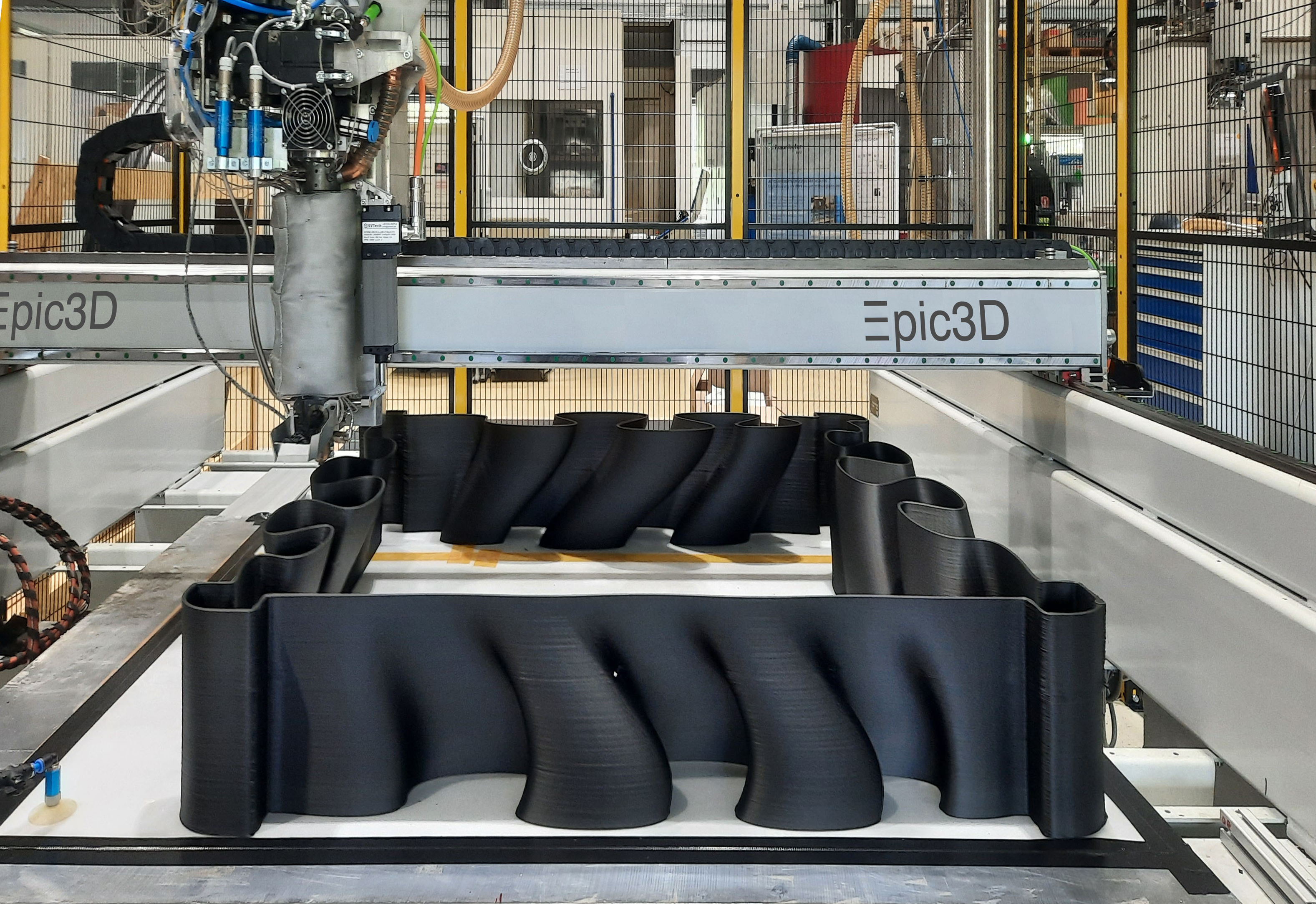
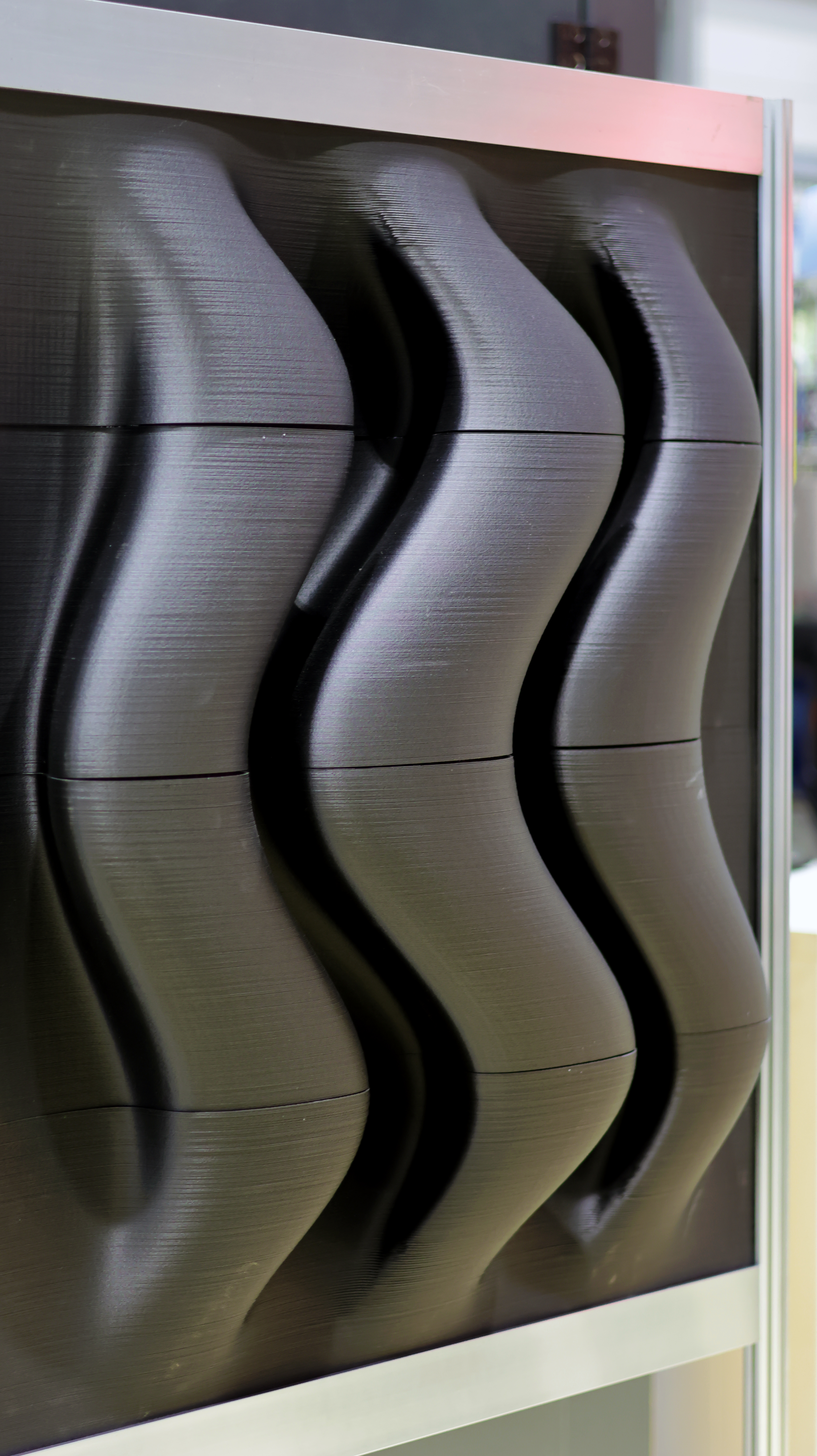
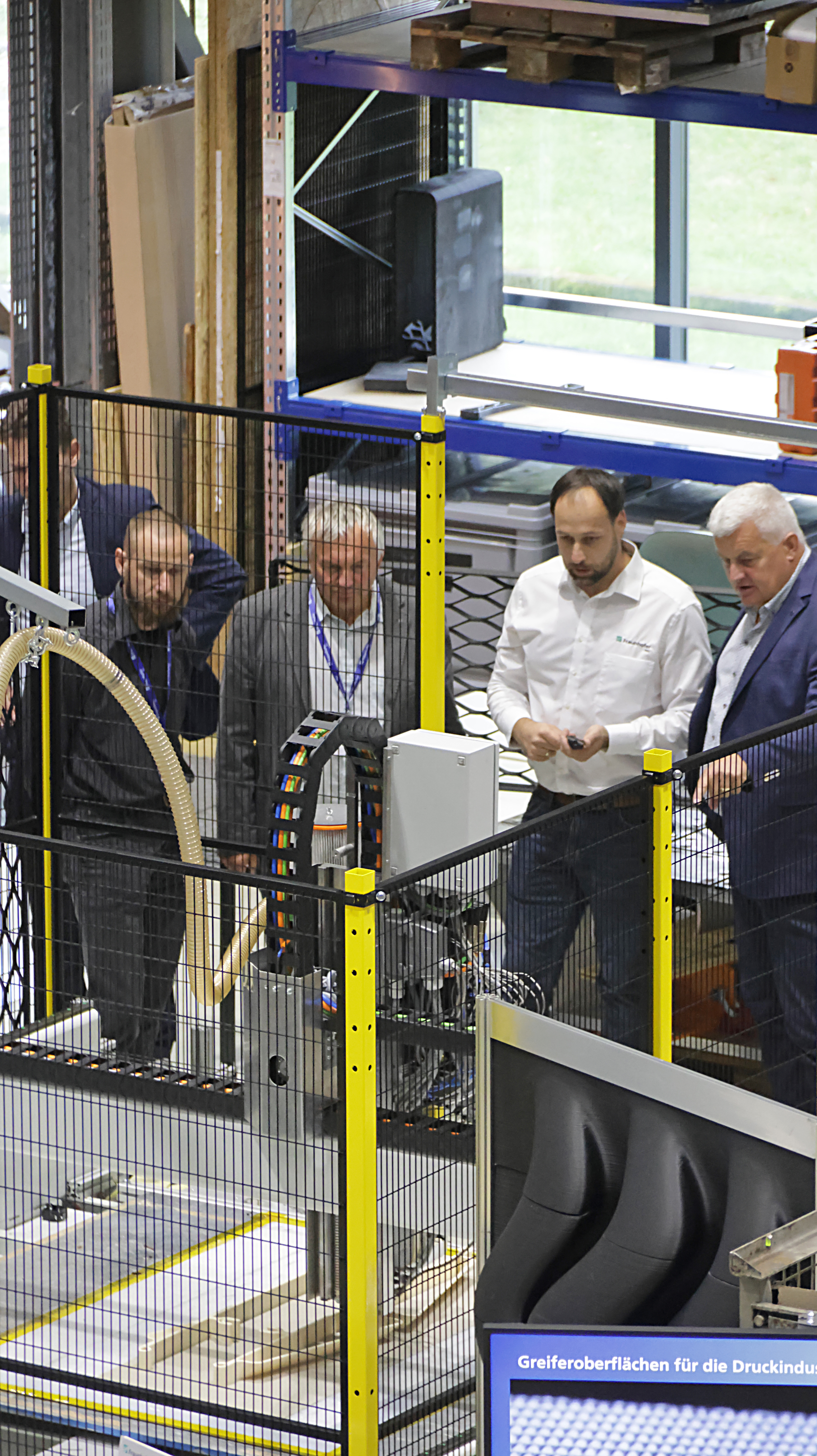
Attractive Facade Elements, Fences, and Gates
When it comes to more complex designs, such as facade elements with different textures or custom shapes like a company logo, 3D printing can fully demonstrate its advantages. Until now, the main limitations of additive manufacturing have been the size of the build platform and the slow, expensive processes that rely on filament rather than granules as the printing material. In collaboration with Wirth & Co. GmbH, Fraunhofer IWU banks on large-format components for the building sector, like customizable facades. Likewise, the SEAM process could also be a good choice for producing fences or gates, as it offers high quality, cost efficiency, and fast production times. The partners emphasize that their plastics will meet all fire safety requirements and UV and weather resistance standards.
Affordable Customization
The SEAM printing process works by drawing in and plasticizing granules through a modified extrusion screw. The resulting plastic melt is deposited layer by layer onto the build platform. This tool-free manufacturing process makes custom designs affordable: Unlike fiber lamination or forming processes, there is no need to produce a mold; the use of colored material safes coating steps. High printing speeds also help reduce costs. Dr. Martin Kausch, head of the Department of Sustainable Fiber-Plastic Composites at Fraunhofer IWU, emphasizes, "We make sophisticated design affordable. The personal touch in facade design is, of course, also achievable in traditional manufacturing. But only with processes like SEAM is it cost-effective." Florian Stöckel, managing director of Wirth & Co. GmbH, adds, "With 3D printing in the SEAM process, completely new design possibilities are opening up in facade construction. Together with Fraunhofer IWU, we are optimizing design, materials, and the 3D printing process for applications in the construction industry. With our investment in the Epic3D portal system, we are making additive manufacturing fit for building components."
The SEAM Team: Epic3D, METROM P1410, and SEAMHex
Fraunhofer IWU has developed all three systems at the SEAM Research Center in collaboration with Metrom and 1A Technologies UG and are masters of extrusion-based 3D printing. While Epic3D stands out with its 2-meter-long and 1.7-meter-wide build platform, the METROM P1410 also allows additional processing steps like milling. System n° 3, the SEAMHex, relies on the hexapod – a swiveling 6-axis parallel kinematics system that provides the build platform with exceptional movement flexibility. The main characteristics of this movement system are high dynamics, low moving masses, and, as a result, high positioning and path accuracy. SEAMHex produces medium-sized components quickly and precisely.
Fraunhofer IWU at Formnext, Frankfurt am Main, November 19-22, 2024
Dr. Martin Kausch's team will present the latest research findings on the SEAM process at the Formnext trade fair: Hall 11.0, Stand E38, and Hall 11.0, Stand C29 (Metrom).
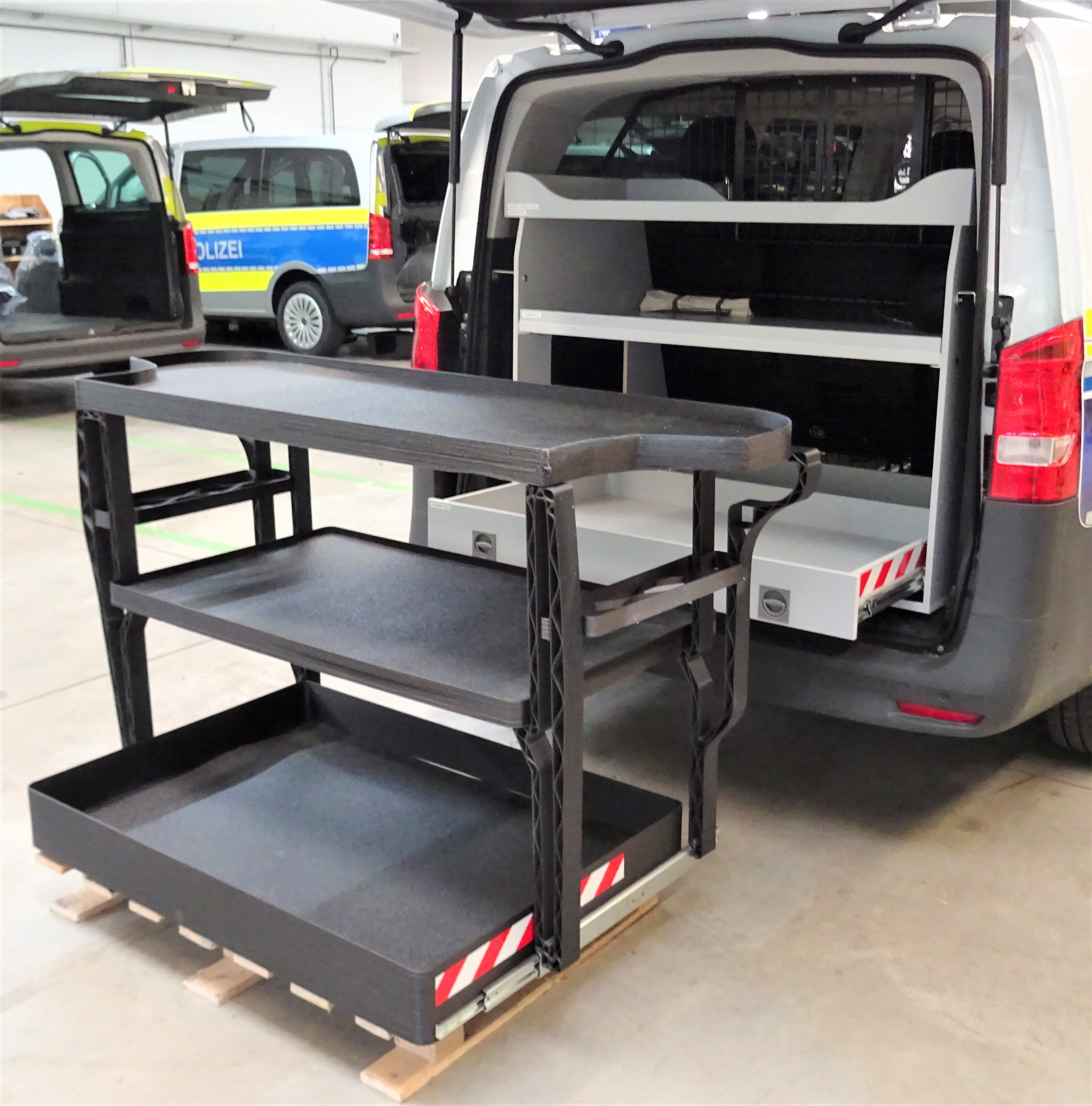