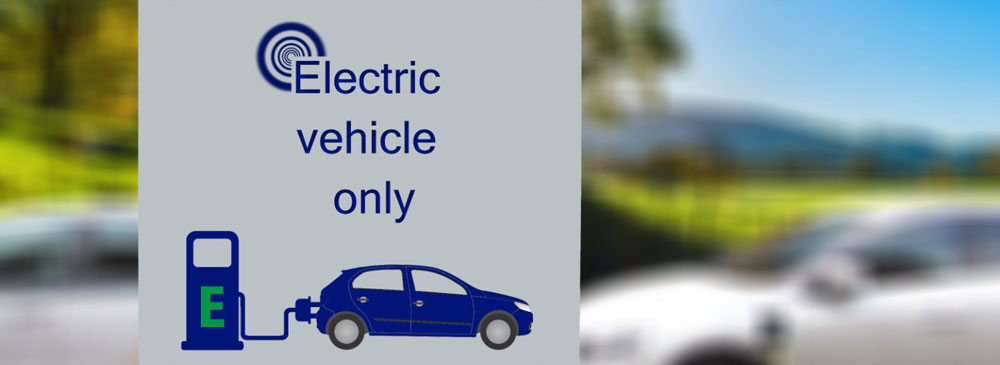
Range and charging capacity are the key to the acceptance of electromobility among customers. The competitiveness of manufacturing companies ultimately depends on this. Important elements of a battery system for electric cars are not only the battery module itself with its cells, but also the housing with structures for load distribution and temperature regulation, frames, covers and base plates, which together must protect against overheating and prevent damage to the battery core in the event of an accident.
Together with partners from research and industry, we are demonstrating in the “COOLBat” project how innovative design principles, materials and production processes can help to manufacture housings for these battery systems in a climate-friendly way and at the same time integrate better performance characteristics.
The project focuses on the development, optimization and scaling of lightweight materials and technologies. In order to bring together the individual developments and evaluate them in terms of resource efficiency and lightweight construction, the battery system of an electric vehicle is chosen as an application example and demonstrator. These battery systems represent a central innovation component of sustainable mobility and are crucial for the competitiveness of electrically powered vehicles made in Germany.
The excellent transferability of the results, which are generated on the basis of individual lightweight components and the overall system, to other sectors is a declared goal of the project partners. The life cycle analysis is carried out throughout the entire development process. The consideration of the results in each project phase leads to CO2-reduced material and technology selection and sustainable product performance over the life cycle. Mass savings through new design principles are realized by combining subsystems into functionally integrated structures, such as the casting integration of cooling lines in support structures or the integration of cooling lines and crash absorption systems in an underbody sandwich structure using energy-absorbing aluminium foam core materials.
By using load-path-compatible fibre-plastic composites in the form of Towpregs, the use of materials with a high CO2 impact (carbon fibres) is to be minimized. Mass savings through new materials are achieved by developing geometrically flexible heat-conducting materials with adjustable properties. These are intended to replace energy-intensive, ecologically highly polluting and cost-intensive heat-conducting pastes. CO2 savings through integral production processes are being sought through the casting production of support structures with integrated fluid guide structures and the integral production of flat support structures with a crash intrusion protection function. By reducing the number of individual systems in conjunction with integral manufacturing processes, cost- and mass-intensive interfaces and the number of energy-intensive joining technologies can be reduced. As a result, energy can be saved in the manufacturing and assembly process and CO2 emissions can be reduced due to a lower total mass during the utilization phase. In addition, intumescent foams based on lignin are being investigated for the realization of fire protection.
Finally, a demonstrator will be used to demonstrate the functionality of the developed materials and the feasibility of the designed processes. This will make the research results more visible and increase acceptance and trust among users.
Term:
2021 - 2024
Coordination:
Fraunhofer IWU
Project Partner: