Fraunhofer IWU at Automatica 2023, Hall A4 Booth 321
Quality forecasts in production: reliable and real-time thanks to Artificial Intelligence
What about predicting with high certainty whether a component meets the quality requirements even while a machining step is in progress? Artificial Intelligence (AI) makes it possible. The AI solutions developed at Fraunhofer IWU represent an improvement over previous in-line inspection systems, eliminating the need for time-consuming removal for testing purposes. Such quality forecasts during processing can be integrated into many industrial manufacturing processes, often in combination with existing, cost-effective sensors. However, this AI can also be used for optimization purposes. It can help control process input parameters, such as avoiding scrap from the outset or reducing energy consumption in production without compromising quality.
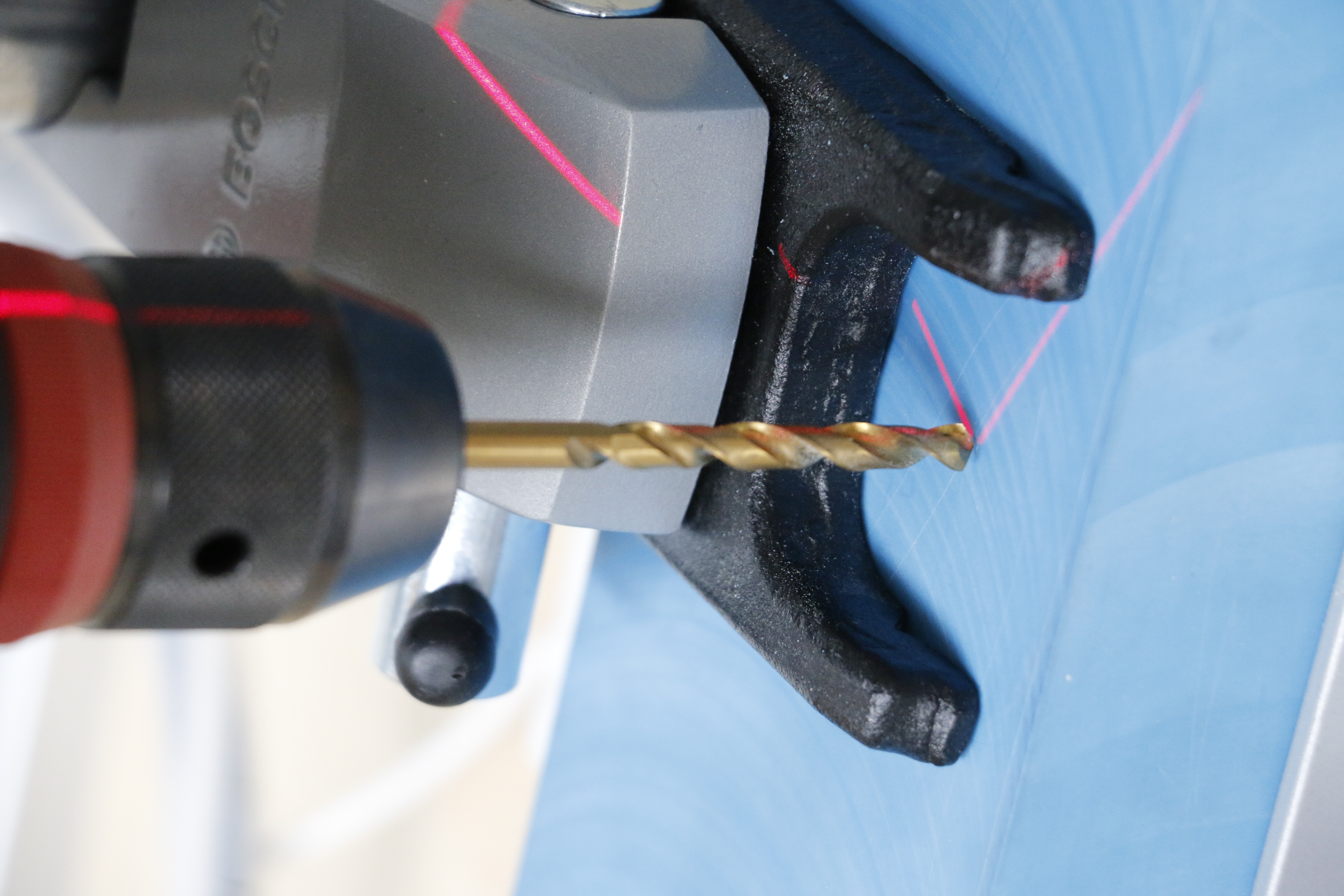
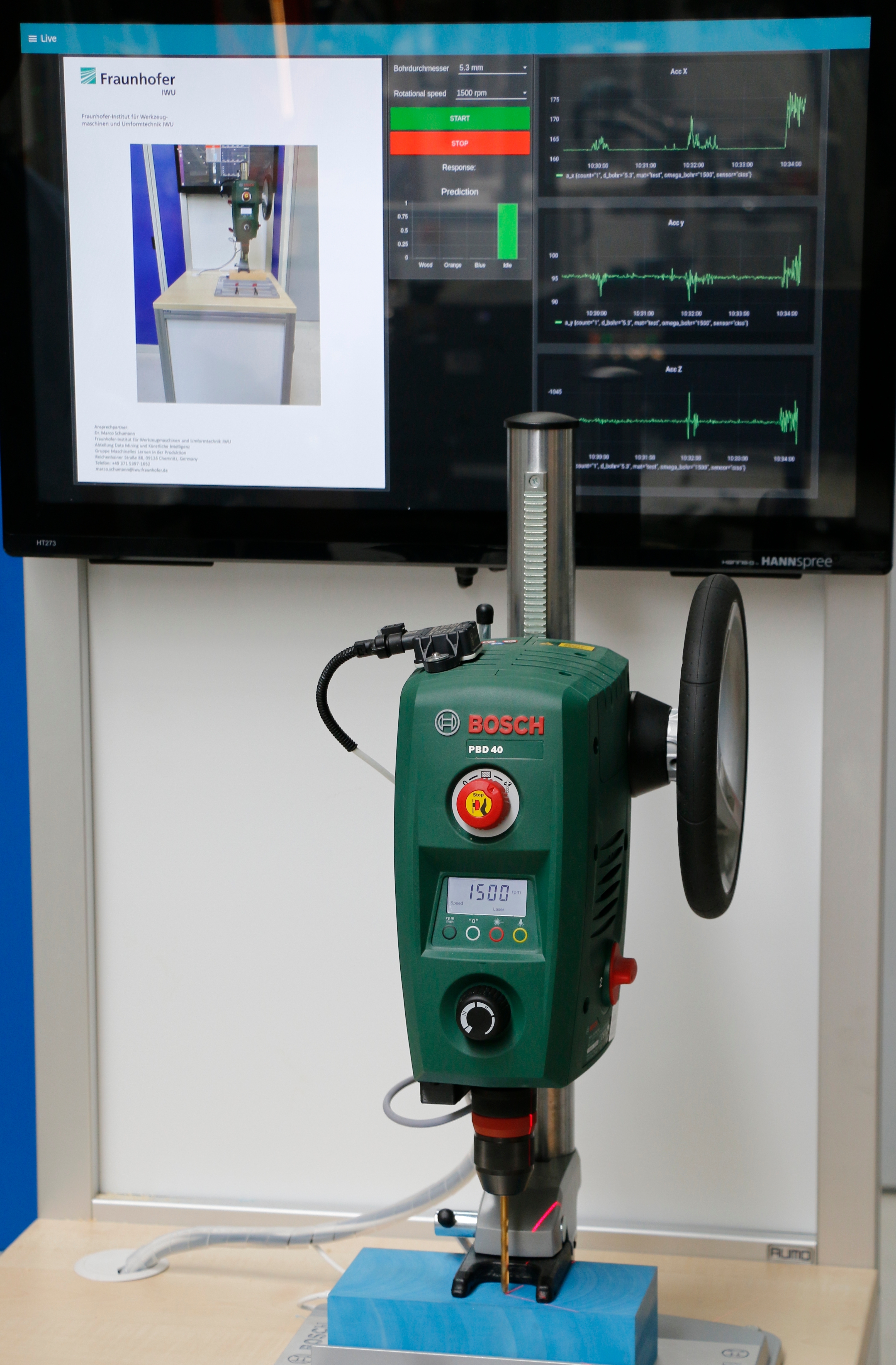
Quality forecasts
Typical future application areas for the newly developed AI solution include machining steps such as drilling, turning, and milling. In drilling, for example, rotational speed, feed rate, and measurements from a vibration sensor provide information about the expected qualitative result. This allows obtaining a quality assessment, for instance, in deep-hole drilling without the need to destroy the workpiece for measurement.
Process optimization
In the field of metalworking, the use of AI has proven particularly effective in warm forming. In this process, the workpiece is heated in the oven above the austenitizing temperature (approximately 880 °C) before pressing. Once the desired target temperature for optimal hardness is reached, the hot sheet metal is placed into the press and formed. This results in a martensitic structure, thus hardening the material. Since product quality is paramount in this energy-intensive process, the furnace temperature is often set higher than necessary. By forecasting the anticipated hardness, AI provides data-driven guidance for fine-tuning the hardening temperature.
In injection molding processes, AI monitors specific parameters such as the mold temperature, the rotational speed of the screw for the granulate, the melting temperature, the mold holding time, and the cooling time. Timely countermeasures based on unfavorable quality forecasts help significantly reduce scrap.
100% inspections, low number of training datasets
In all application scenarios, AI can be directly used in the manufacturing process (in-line) to monitor the entire batch through 100% inspections. Random sampling inspections are thus a thing of the past.
For training various AI models, in many applications, a double-digit number of datasets is sufficient, supplemented with process expertise. In operation, the computing power of (local) edge computing is often sufficient.
Together with Synapticon GmbH, Fraunhofer IWU presents a new architecture for Human-Robot Collaboration (HRC)
Robots intended for HRC (Cobots) have particularly high requirements for the safety of their motion sequences. The central safety module must process data from numerous sensors, which requires many cable connections for sensors and actuators in traditional robot architectures and proprietary solutions. The new safety architecture developed by Fraunhofer IWU, NexCOBOT, and Synapticon GmbH is designed to be decentralized, enabling safe collaboration between humans and industrial robots even when the work situations dynamically change, with significantly reduced cabling effort. Only power and communication connections need to be routed to the drives. Another advantage is that by monitoring the safety of motion sequences directly at the drive axis, significantly less reaction time elapses. The new solution can be seen at the Synapticon GmbH booth at Automatica.