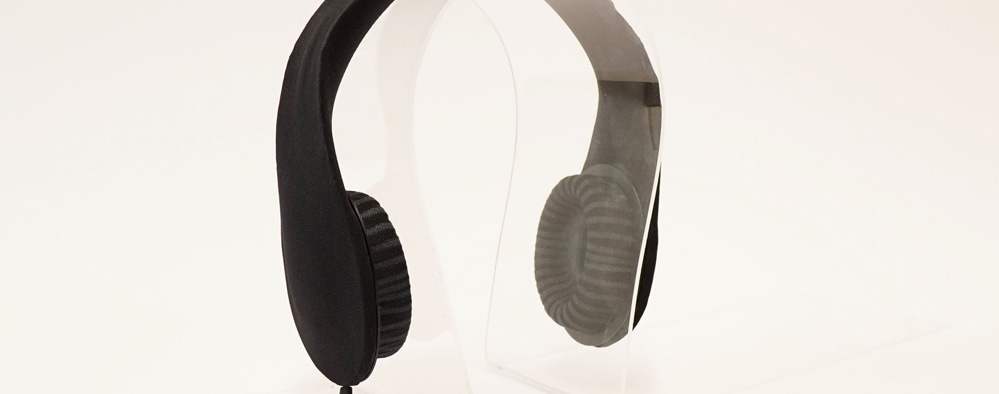
How we design products is largely determined by the tools available for manufacturing. The prevailing methods shape our perception of an object. We asked ourselves whether the transfer of experimental process techniques is sufficient to shake up the image of a consumer product. The project aimed to manufacture headphones in a fully automated process by combining textiles, additive manufacturing, and the functional integration of electronics.
When textiles are pre-tensioned and connected to a rigid component, intrinsic forces arise, leading to a defined deformation. This effect can be achieved by subjecting a fabric to directed tension. A structure can be printed onto the resulting 2D surface using FFF printing, which binds to the fabric. The WEAM process can simultaneously apply conductor structures, functional elements, and electrical components. This way, an unfolded version of a headphone is created. When the external pre-tension is removed, it results in the targeted transformation into the final shape of the headphone in its ready-to-use state.