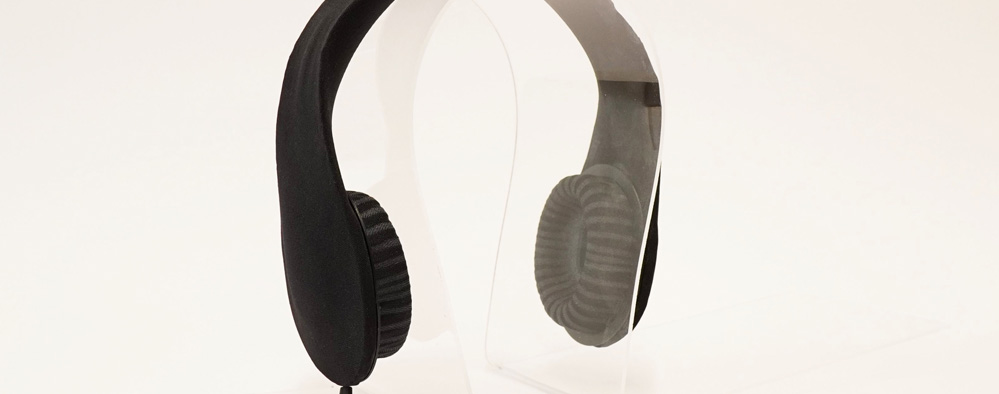
Wie wir Produkte konzipieren, hängt maßgeblich davon ab, welche Werkzeuge uns für die Fertigung zur Verfügung stehen. Die vorherrschenden Verfahren bestimmen dabei, wie unser Bild von einem Objekt ist. Wir haben uns die Frage gestellt, ob die Übertragung von experimentellen Verfahrenstechniken bereits ausreicht, um das Bild eines Konsumprodukts aufzurütteln. Im Vorhaben sollte durch die Kombination von Textil, additiver Fertigung und funktionaler Integration von Elektronik ein Kopfhörer in einem vollautomatisierten Prozess gefertigt werden.
Wenn Textilien unter Vorspannung mit einem steifen Bauteil verbunden werden, ergeben sich intrinsische Kräfte, die zu einer definierten Deformation führen. Dieser Effekt lässt sich erzeugen, indem ein Stoff unter gerichtete Spannung gesetzt wird. Auf die sich ergebende 2D-Fläche kann mittels FFF-Drucks eine Struktur aufgedruckt werden, die sich an den Stoff anbindet. Durch das WEAM-Verfahren können gleichzeitig noch Leiterstrukturen, Funktionselemente und elektrische Bauteile aufgebracht werden. So wird eine aufgeklappte Version eines Kopfhörers hergestellt. Beim Entfernen der äußeren Vorspannung kommt es zur gezielten Umformung in die Endform des Kopfhörers im einsatzbereiten Zustand.
Die Form wird durch das Aufbringen dünner Kunststoffstreifen auf vorgedehnte Textilien erzeugt. Die aufgebrachten Kunststoffbahnen bilden ein zweidimensionales Endoskelett auf dem Textil, in das beim 3D-Druck elektrische Komponenten integriert werden können. Die dreidimensionale Form entsteht durch die anschließende Relaxation des Textils. Die Variation des Endoskeletts sowie der textilen Vorspannung ermöglicht eine individuelle Form, Steifigkeit und Funktionalität der Struktur.