Messe München, June 24–27, 2025, Booth A4.319
One-Stop-Shop for Plant, Machinery, and Vehicle Manufacturing: Fraunhofer autoMOBILproduction Alliance Presents an Attractive Package at automatica
Focusing on self-optimizing systems, flexible and adaptable factories, human involvement in production, and agile process chains, the 17 institutes of the Fraunhofer autoMOBILproduction Alliance are strong industrial partners. At automatica, the Alliance will present clever automation solutions, including quality assurance, hands-on VR and AR applications, and highly robust sensor systems for process control.
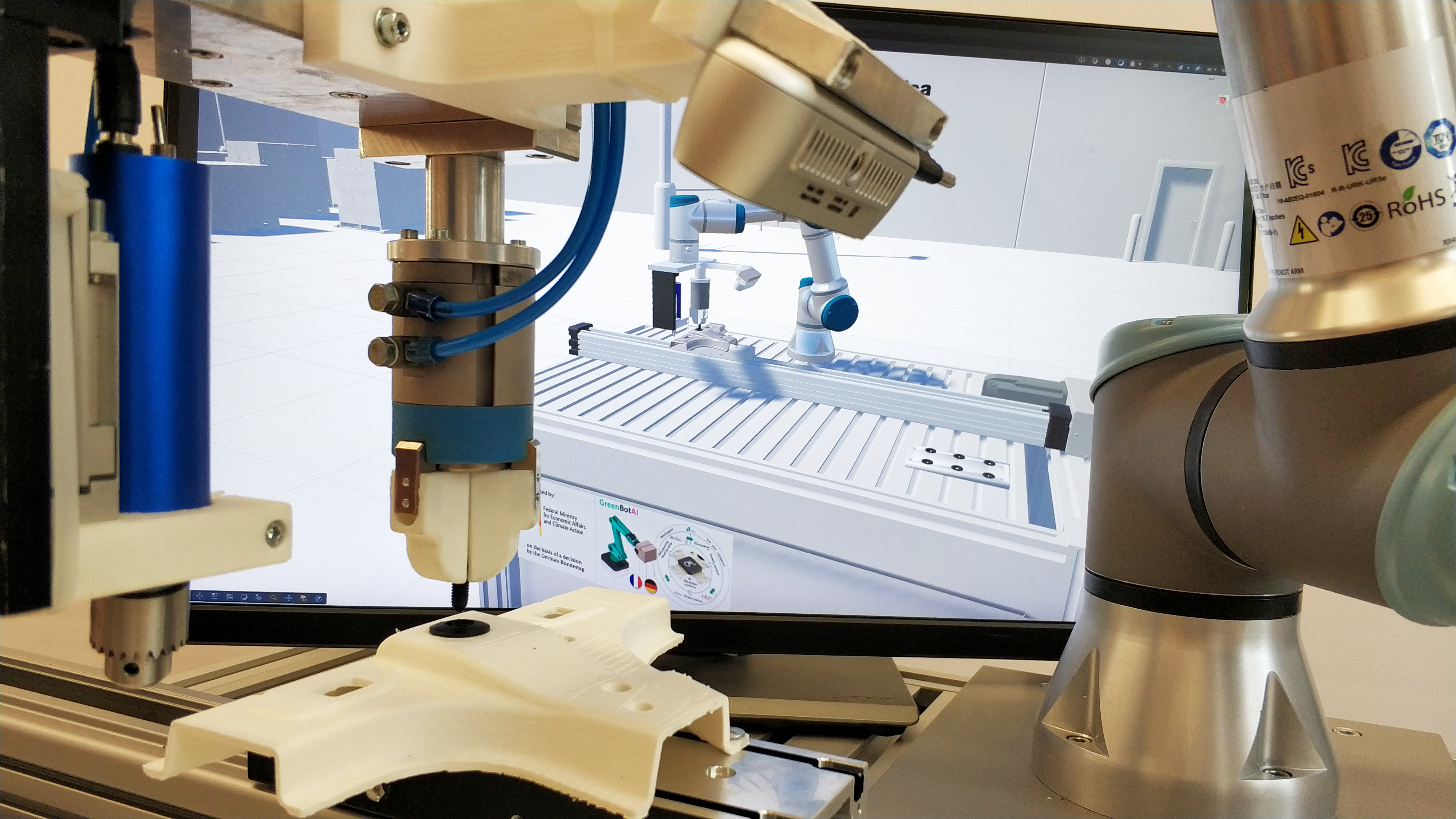
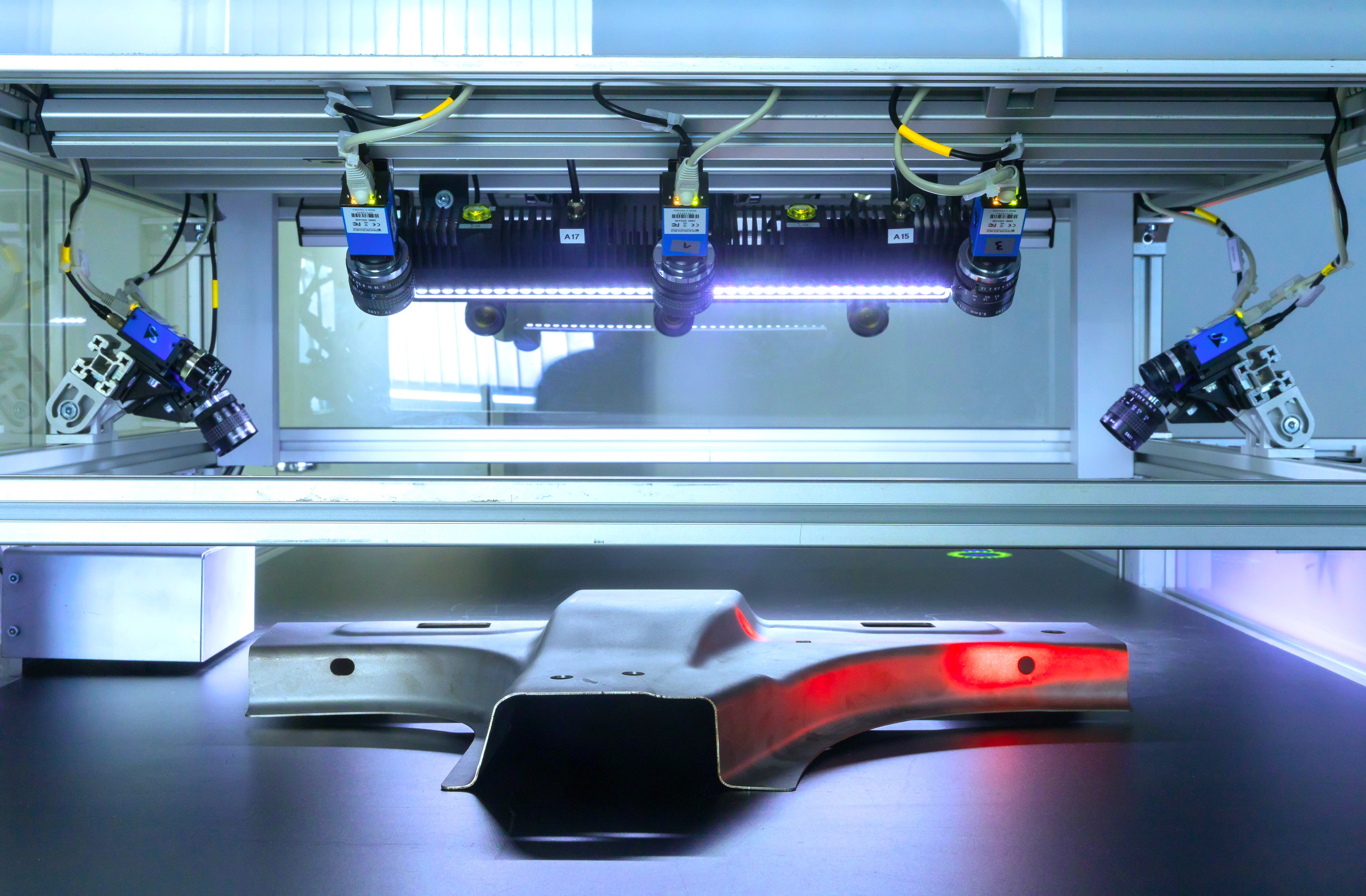
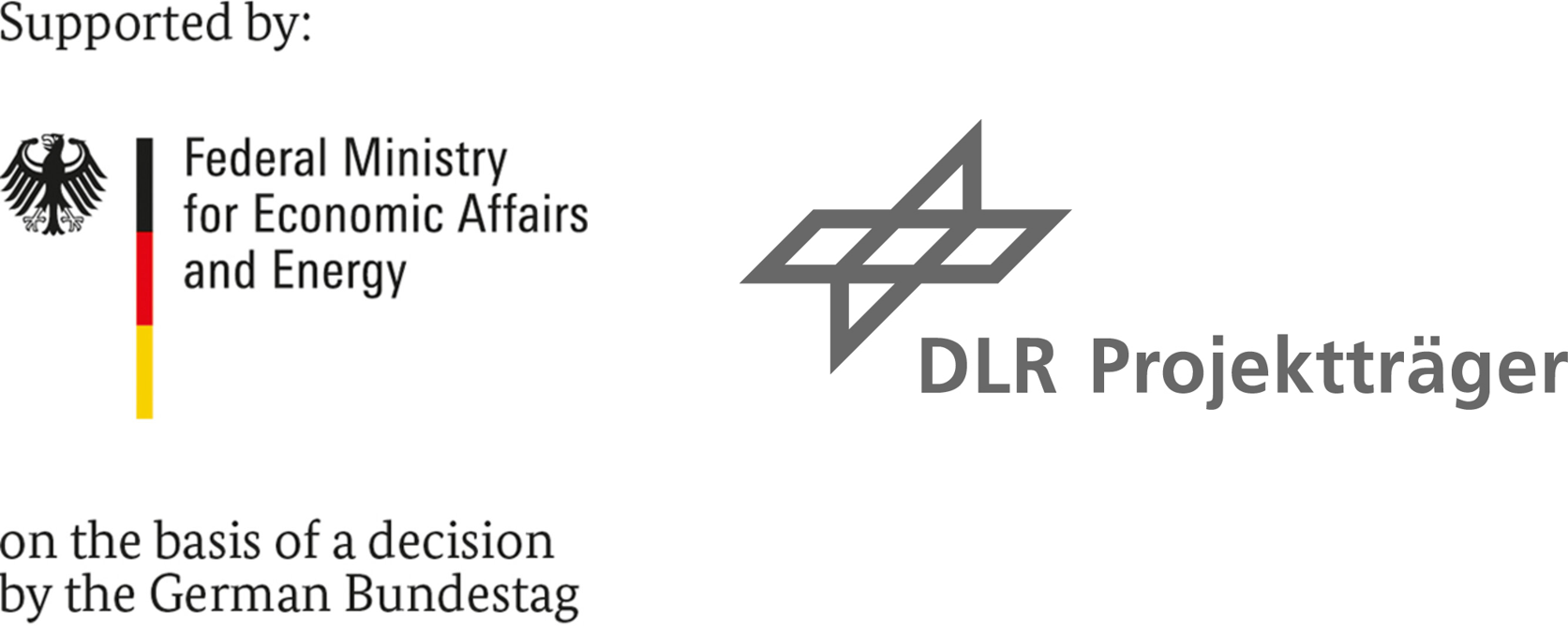
GreenBotAI Makes Robots More Flexible While Reducing Energy Consumption by Up to 25 Percent
Smaller batch sizes instead of mass production, more complex production lines, increasing competitive pressure, and unstable supply chains: it is in this economic context that the German-French research project GreenBotAI focuses on robotics. The project pursues three key goals: ensuring uninterrupted production even in times of crisis, strengthening Europe’s autonomy in production automation, and significantly reducing the energy consumption of robotic applications in European factories.
GreenBotAI addresses technical aspects such as industrial robots’ response and latency times, optimized path planning, and performing tasks “on the fly” during robot movement. For example, this enables capturing images for object recognition without stopping, streamlining handling and assembly tasks. The Fraunhofer Institute for Machine Tools and Forming Technology IWU is the lead coordinator in this project.
Reducing Energy Consumption Without Replacing Robots
GreenBotAI employs several levers to reduce energy consumption by up to 25%. These include lightweight AI models, accelerated gripping tasks, and reduced computational load.
Controlling Complex Movements with Simple Image Data
A single 3D image of a component, captured by an industrial camera and requiring minimal computing power, enables the robot to pick up, inspect, and correctly position the part. The system can now even handle joining parts on moving conveyor belts.
In the automatica demo setup, the control software determines the position of all objects relative to the robot based on image data, calculates the robot path, and selects a grip point. The robot then picks up a blind rivet from a magazine. These fasteners are commonly used in the automotive industry to secure trim parts. The robot grips the smooth, cylindrical end of the rivet and tracks the motion of a B-pillar base on the conveyor system before the robot inserts the rivet into the B-pillar base. There is no communication between the robot and the conveyor; predicting its movement using image data is sufficient. Real-time force analysis then guides the robot in pressing the rivet into the part.
This process uses the latest AI that mimics the human sense of touch. A digital twin visualizes all real-world robot actions. The Fraunhofer IWU-developed software Xeidana® handles final quality control; it verifies whether the robot has inserted the rivet correctly.

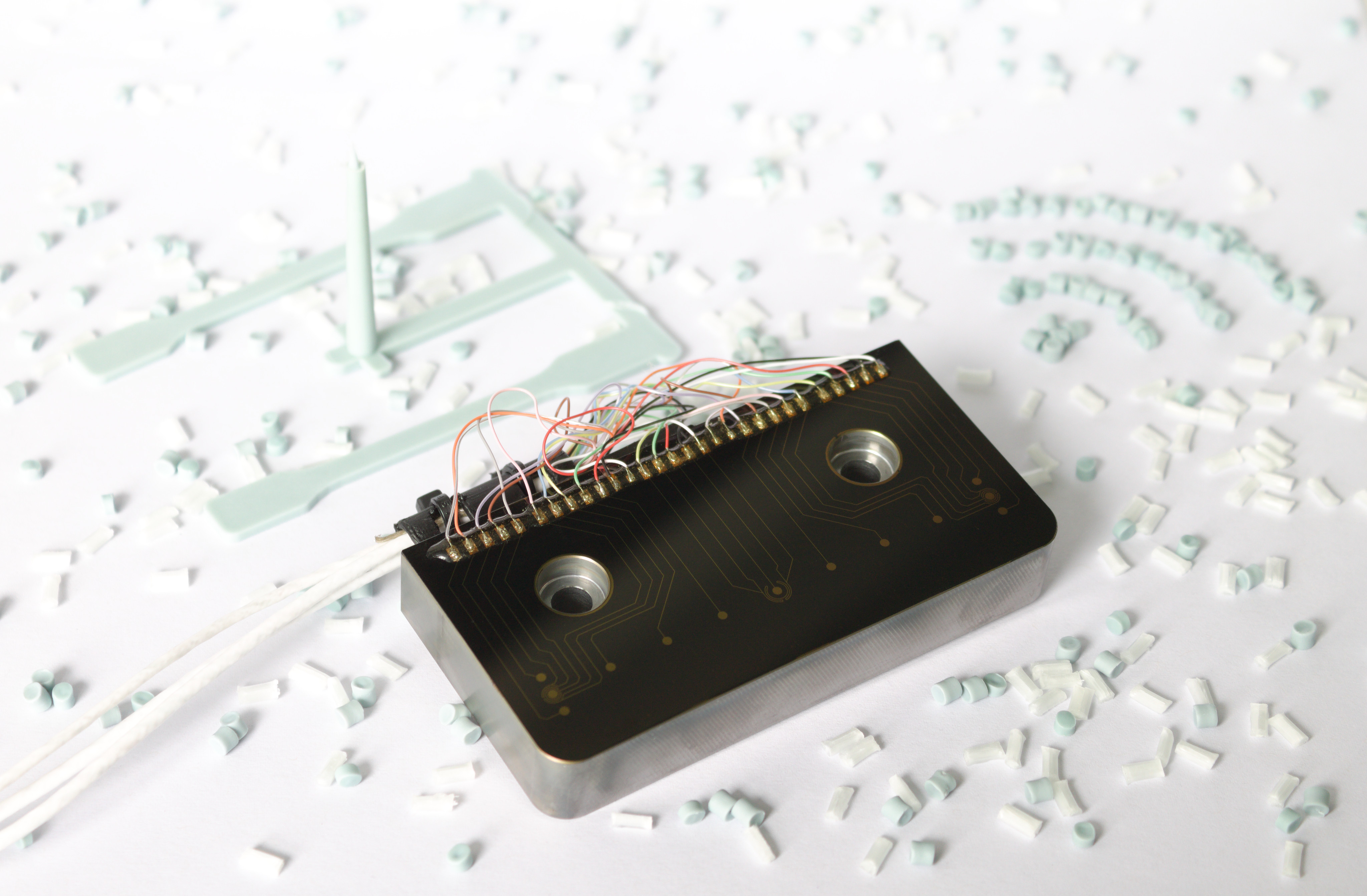
Intuitive Planning of Assembly and Disassembly with Physically Accurate Simulations and XR Support
Planning assembly and disassembly processes — especially when using flexible parts such as cables, hoses, or flexible sheet components — presents specific challenges. In early development phases, physical prototypes are often unavailable to assess factors like spatial accessibility, feasibility, or risk of damage during installation or removal.
Extended Reality (XR) environments, combining virtual and augmented reality, offer a powerful and intuitive solution by simulating flexible components with physical accuracy. Virtual planning saves time and costs by reducing the need for expensive physical prototypes and enabling faster iterations. This approach shortens development cycles significantly. Intuitive XR tools also grant early access to the design process for cross-functional teams, including assembly workers and technical experts.
Thanks to integration with advanced graphics engines like Unity, Unreal Engine, or NVIDIA Omniverse, professionals can explore complex assembly scenarios interactively and immersively using the IPS Cable Simulation software developed with contributions from the Fraunhofer Institute for Industrial Mathematics ITWM.
More information: Cables, Hoses, and Flexible Structures – Fraunhofer ITWM
Sensor Systems with Thin-Film Sensors for Monitoring Production Processes and Tool Wear
The Fraunhofer IST showcases innovative thin-film sensors that are applied directly onto tool surfaces, enabling spatially resolved, real-time temperature measurement in critical stress zones of injection molding processes.
As part of Industry 4.0, accurate monitoring of key parameters such as temperature and pressure curves in plastics processing is vital. The tool insert on display includes 13 sensor points that monitor the flow front during the molding process. Due to the high durability of the thin-film system, it is possible to continuously monitor even processes involving high glass fiber content or recycled materials — a critical step toward sustainable material uses in circular production.
A newly developed electronics unit reads and analyzes the data in real time. AI accurately predicts part quality before the mold opens, enabling quick process adjustments and optimization.
More information: Sensors – Thin-Film Sensors for Industrial Applications