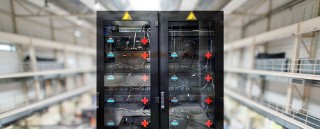
Eine Umfrage unter Maschinen- und Anlagenherstellern ergab, dass zur Grundlastoptimierung und Absenkung von Lastspitzen noch einiger Forschungsbedarf besteht. Unterschiedliche Anwendungsszenarien und Maschinentypen müssten betrachtet werden, um eine maschinenoptimierte Auslegung dank passender Algorithmen zu erreichen, Energiespeicher optimal auszulegen und bestmöglich ausnutzen zu können. Auch die jeweils passende Energiespeichertechnologie solle berücksichtigt werden. Dieser Problematik nimmt sich das vom Bundesministerium für Wirtschaft und Klimaschutz geförderte Projekt »Energiespeicher in der Produktion« (ESiP) an.
mehr Info