In order to reduce the CO2 footprint per vehicle by at least 25 percent
ZEvRA is developing solutions for a circular electric vehicle and increasing the use of recycled materials
By 2035, the EU aims for new vehicles to be manufactured almost entirely of recycled, refurbished, repurposed, repaired, or reused parts, with the share of new raw materials needed for car production approaching zero. The result will be over 1.5 tons of material per vehicle saved. Of course, from 2035 on, new cars will still have to meet all crash safety requirements and satisfy customer expectations regarding quality. Under the leadership of Fraunhofer IWU, a consortium of 28 European partners, including five automakers (OEMs), is now showcasing pathways towards a consistently resource-efficient production in the EU project ZEvRA. The partners aim to develop a virtual Circular Car Concept based on a popular Skoda model; for demonstration purposes, they will assemble a vehicle with parts made from recycled materials that comply with the principles of the circular economy.
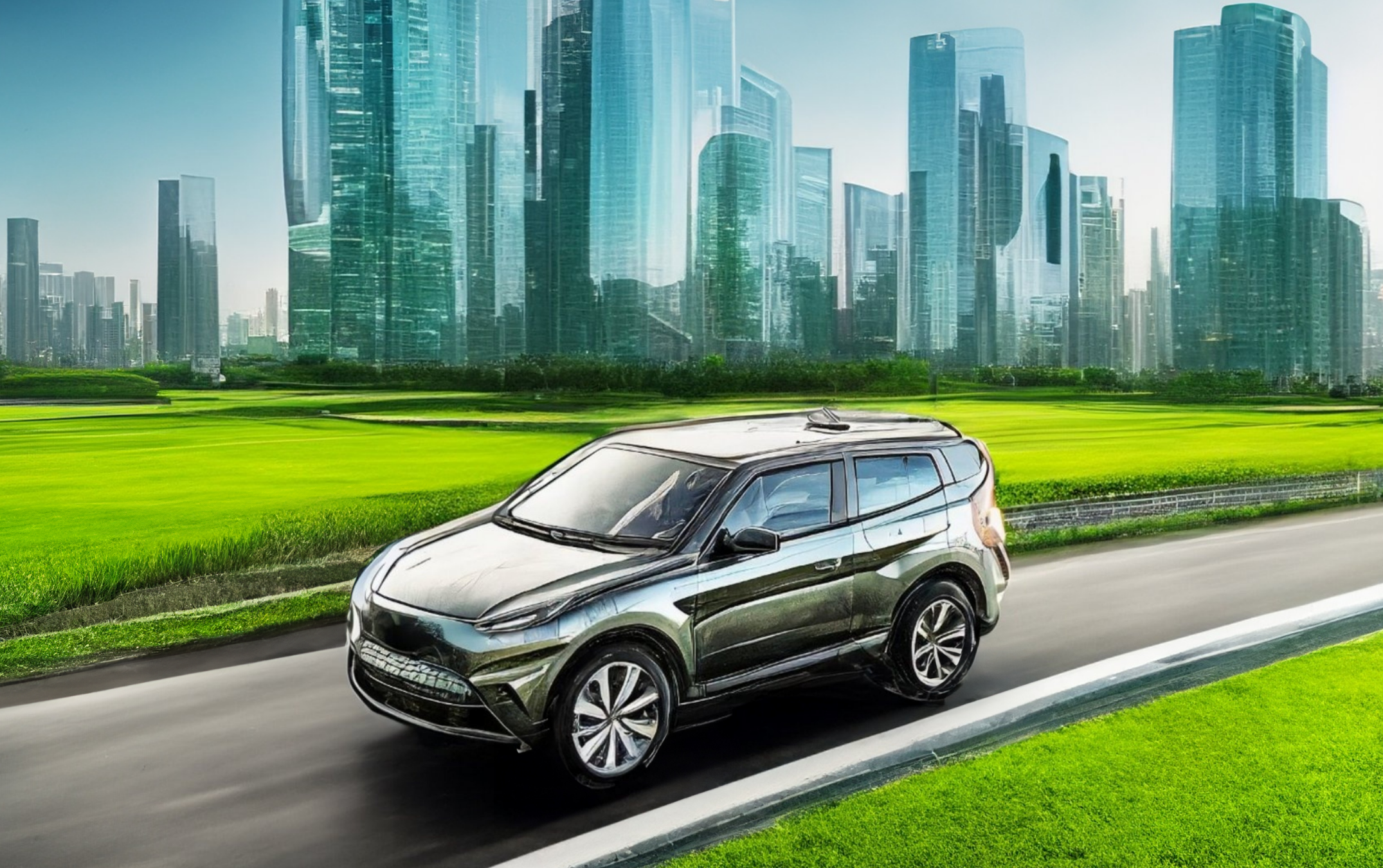
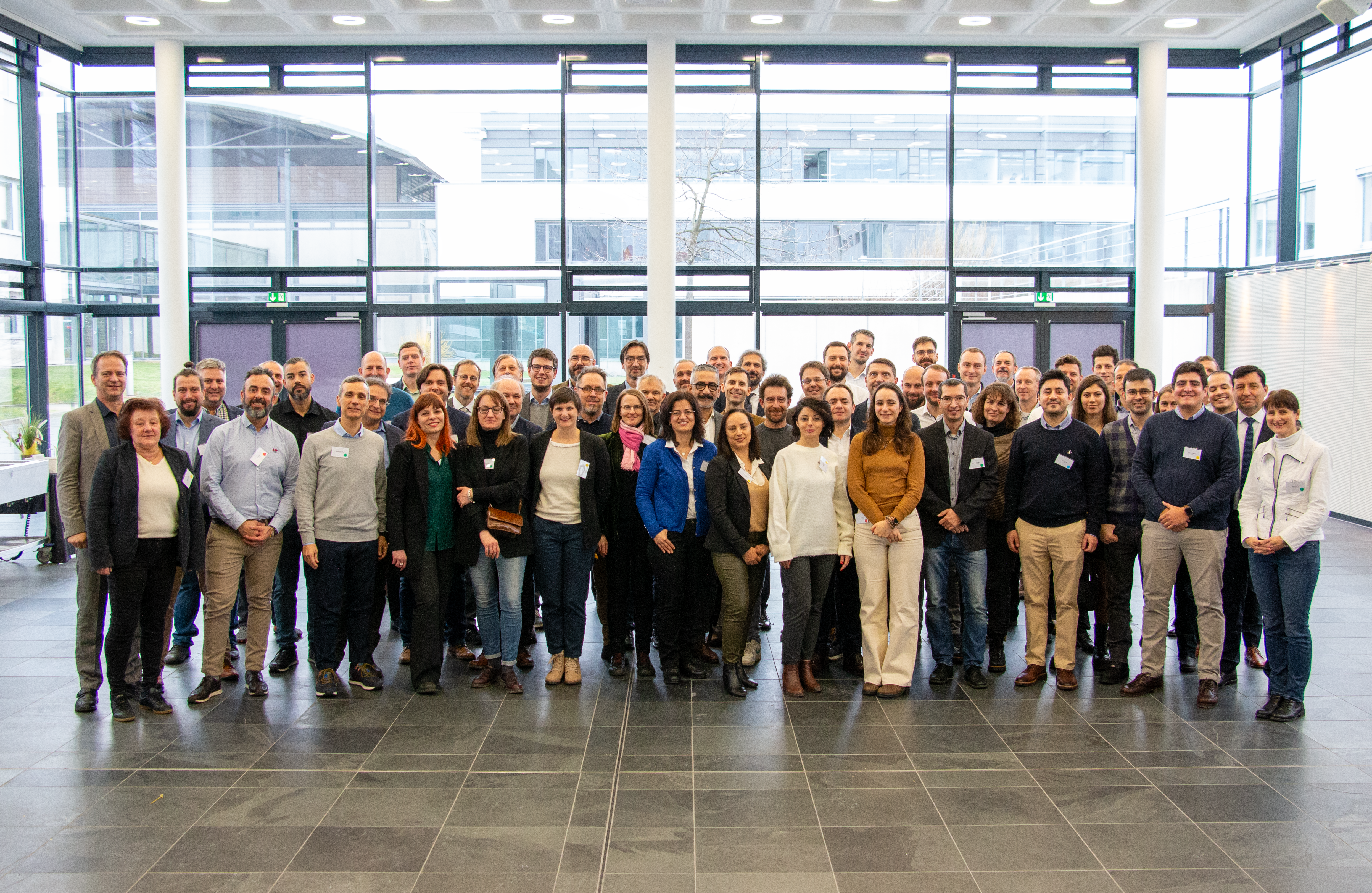
Starting in 2035, operating a new vehicle in the EU may no longer cause CO2 emissions. From today’s perspective, most new cars will then be battery-electric. However, producing battery-electric vehicles means significantly higher CO2 emissions when compared to manufacturing cars with internal combustion engines. As battery-electric vehicles should have no worsening overall impact on climate, it is crucial to consider the entire value chain, from material provision and manufacturing to end-of-life processes. To this end, ZEvRA will develop a methodology for Design for Circularity and a holistic circularity assessment. ZEvRA will concentrate on relevant materials covering more than 84 percent of the material mix of a typical electric vehicle: steel, aluminum (rolled, cast, and foamed), thermoplastic composites, plastics, glass, tires, and rare earths. The solutions to be developed will require support from a range of digital tools to ensure circularity, traceability, and the virtual integration of components into a fully reproducible vehicle. Thanks to ZEvRA, the CO2 footprint per vehicle will decrease by at least 25 percent in the future.
Share of "make new parts from old ones" will reach 100 percent for some material groups
A 100 percent reuse rate for numerous materials like steel and all aluminum alloys in rolled, cast, and aluminum foam parts: This is what the goal of manufacturing a substantial number of vehicle parts without new raw materials means. Even for new tires, almost exclusively secondary raw materials are to be used, including for the tread. Obviously, Design for Circularity, i.e., considering reprocessing criteria as early as in the phase of developing new parts, makes the most significant contribution to a sustainable environmental and carbon balance.
ZEvRA: strong alliance for a circular economy in the European automotive industry
In the EU project ZEvRA (Zero Emission electric vehicles enabled by haRmonised circulArity), car manufacturers such as Volkswagen, Skoda, and Stellantis (including Peugeot, Citroën, Opel), and major suppliers (including Faurecia, Continental) have committed to ambitious sustainability goals. Insights and results from the project, scheduled to run until the end of 2026, can thus be widely anchored in the automotive industry and have an impact. The complete list of project partners is available here.
Core competency resource efficiency: Fraunhofer IWU coordinates ZEvRA
The focus of the research and development activities of the Chemnitz institute lies in energy and resource efficiency in manufacturing. In the field of circular economy, IWU works on the constructive and manufacturing prerequisites for a second or third product life for as many products as possible. In ZEvRA, IWU contributes its extensive expertise in repurposing processes for steel components, using aluminum recyclates for kneading, casting, and foam components, as well as the design-accompanying circularity assessment of components.
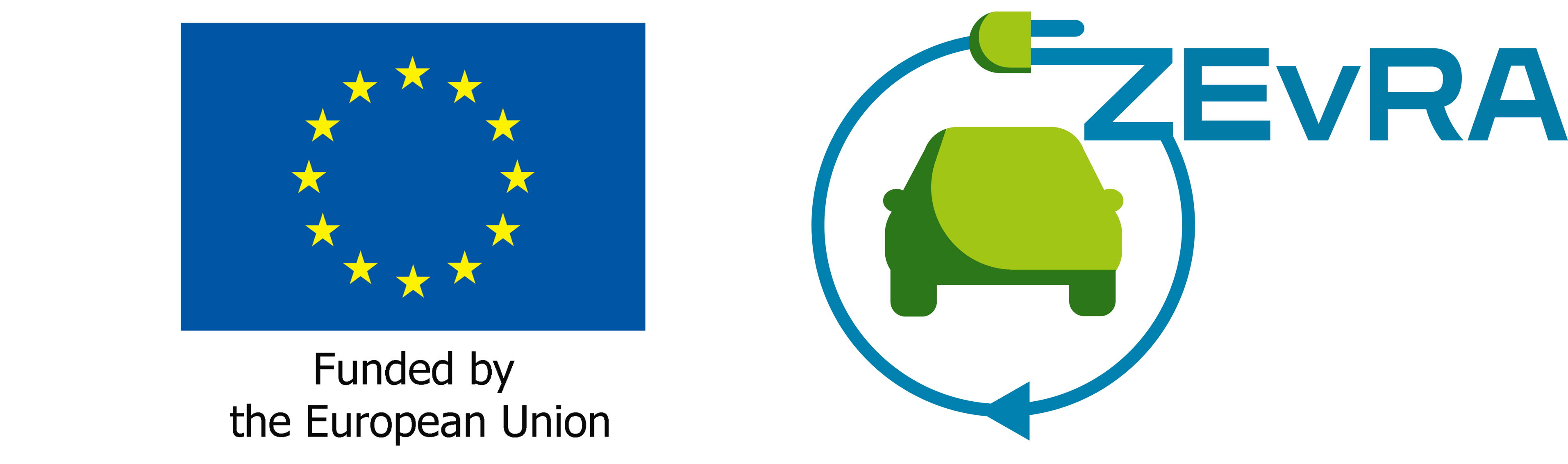