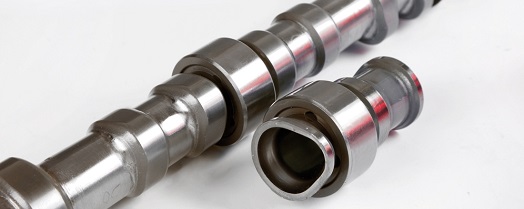
Problemstellung
Die wirtschaftliche Fertigung von Leichtbaukomponenten für den Fahrzeugbau ist eine bekannte und nach wie vor aktuelle Forderung. Auch im Bereich des Powertrains sind massereduzierte Bauteile gefordert, die trotz Gewichtsreduzierung die gleiche Performance über die Lebensdauer erbringen. Ein Paradebeispiel ist die Entwicklung hohler Nockenwellen am Fraunhofer IWU. Seit 1993 fordern immer neue Designs und erhöhte funktionale als auch wirtschaftliche Ansprüche eine permanente Weiter- bzw. Neuentwicklung auf diesem Gebiet.
Lösung
Die Grundidee für die Entwicklung gebauter Nockenwellen beruhte auf der Trennung der funktionalen Anforderungen und der Nutzung angepasster Materialien und Elemente. Für die Momentenleitung kommt ein Rohrhalbzeug zum Einsatz, für den Nockenhub werden einzelne verschleißbeständige Nocken genutzt. Durch umformendes Fügen beim Innenhochdruck-Umformen (IHU) werden die Einzelteile zu einer hohlen Nockenwelle komplettiert, die zusätzlich Endstücke als auch Lagerringe besitzt. Auf Basis dieser Technologie konnten in einzelnen Schritten 55 Prozent Massereduktion und wirtschaftliche Vorteile bei der Prozesskette erreicht werden. Neben dem geringeren Gewicht muss auch wesentlich weniger Material beschafft werden. Derartige Nockenwellen sind seit den 1990iger Jahren im Serieneinsatz.
Die Fertigung präziser und verschleißfester Einzelnocken stell technisch eine Herausforderung und wirtschaftlich einen Kostentreiber dar. Aus diesem Grund wurde ein zweiter evolutionäre Pfad eröffnet und die so genannten monolithischen Nockenwellen entwickelt. Hierbei wird die Nockengeometrie aus dem Grundmaterial des Rohrhalbzeuges ausgeformt. Für den Verschleißschutz der Nocken existieren verschiedene Ansätze. Es können Verschleißschutzschichten thermisch aufgespritzt werden und durch Einsatz vergütbarer Stähle kann die Nockenfläche nitriergehärtet werden. Die neuste Entwicklung beruht auf dem Einsatz presshärtbarer magan-bor-legierter Stähle, welche bereits im Karosseriebau intensiv genutzt werden. Durch die Kombination von IHU und Presshärten lassen sich gegenüber geschmiedeten oder gegossenen Nockenwellen Gewichtsvorteile bis zu 60 Prozent erreichen.