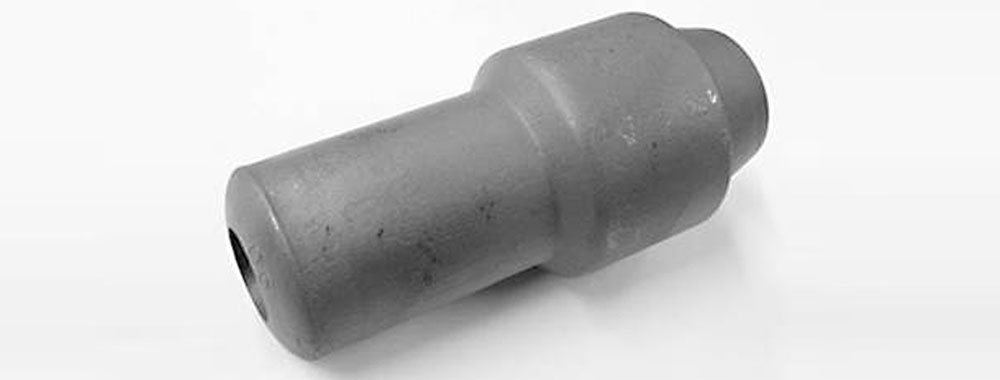
Problemstellung
Umformende Fertigungsvarianten nutzen u. a. Fließpressverfahren zur Herstellung einer hohlen Grundform. Dabei muss berücksichtigt werden, dass die Anwendung des Fließpressens zur Erzeugung einer Hohlform (Napf) stark eingeschränkt ist und demzufolge nur kurze Wellenabschnitte erzeugt werden können. Diese werden anschließend durch die Anwendung eines geeigneten Schweißverfahrens zur Wellengrundform gefügt. Offensichtliche Nachteile dieser Vorgehensweise sind zusätzliche fertigungstechnische Mehraufwendungen, z. B. für Wärmbehandlungs-, Richt- und Wuchtprozesse.
Lösung
Am Fraunhofer IWU wurde die aufeinander abgestimmte Prozessfolge aus Bohrungsdrücken und Fließpressen entworfen, mit der Hohlwellenhalbzeuge bei geringstem Materialverlust umformtechnisch herstellbar sind. In dieser Prozessfolge wird zunächst aus einem Stangenabschnitt durch Bohrungsdrücken ein rohrförmiges Halbzeug umgeformt. Um dieses Halbzeug effizient in eine komplexe Hohlwellengrundform überführen zu können, wird eine Verfahrenskombination aus Hohl-Vorwärts- und -Rückwärts-Fließpressen angewendet. Diese Fließpresskombination stellt in der Prozesskette der Hohlwellenherstellung eine Neuheit dar. Die Anwendung der Verfahrenskombination aus Bohrungsdrücken und kombinierten Fließpressen ermöglicht die weitestgehend spanlose Fertigung einer hohlen Getriebewelle mit einem für die Anwendung in PKW-Getrieben typischen Länge-Durchmesser-Verhältnis. Dabei wird die komplexe Geometrie in nur zwei Fertigungsstufen unter Einhaltung hoher Genauigkeitsanforderungen erzeugt. Zusätzliche Prozessschritte wie Fügen oder Lochen sind für den Herstellungsprozess nicht erforderlich.