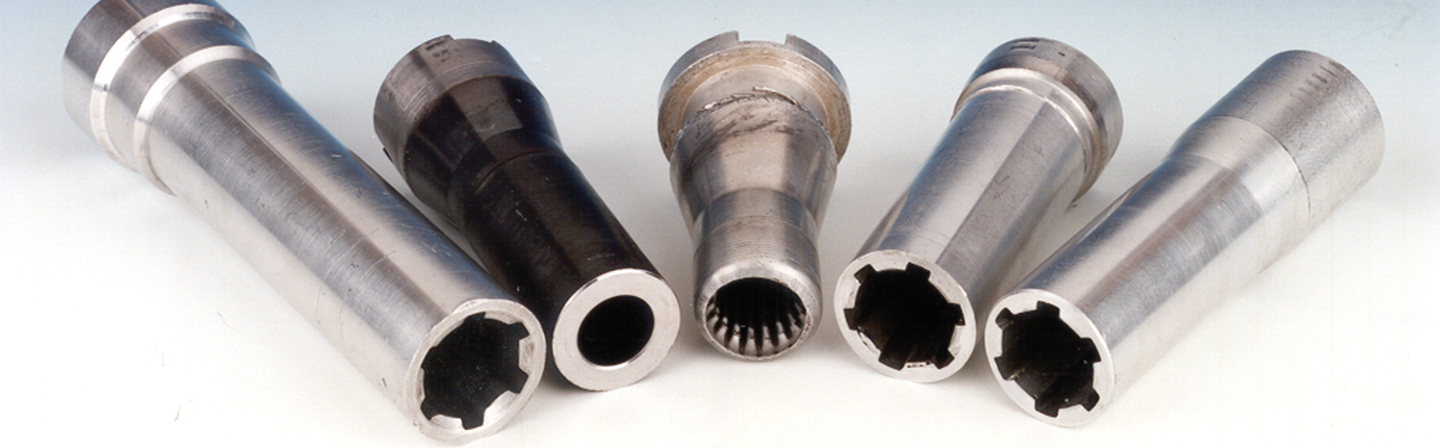
Die Welle im Getriebe eines Autos bietet viel Potenzial für den Leichtbau. Sie wird um fast ein Drittel leichter, fertigt man sie nicht mehr als massives Metallteil, sondern als Hohlform. Das spart Material bei der Herstellung und später Sprit beim Fahren.
Mit einer Erfindung »made in Chemnitz« lassen sich solche Getriebehohlwellen in einem revolutionären Verfahren herstellen: dem Bohrungsdrücken. Dabei handelt es sich um ein inkrementelles, rotatorisches Druckumformverfahren zur Herstellung von Hohlteilen aus Vollzylindern. Einfacher ausgedrückt ist es »Töpfern« mit massivem Metall.
Ähnlich wie der Ton auf einer Töpferscheibe wird ein massiver Metallrohling, der sowohl kalt als auch vorgewärmt sein kann, zum Rotieren gebracht und von mehreren Seiten bearbeitet. Ein Stempel drückt mit einer Kraft von bis zu 2,2 Tonnen in gerader Linie gegen die Stirnseite des zylindrischen Teils. Er verdrängt auf diese Weise den Werkstoff, wie es der Töpfer mit seinen Händen tun würde. Das verdrängte Metall gelangt so nach außen in den Einflussbereich von drei Rollen. Diese drängen es genau entgegen der Richtung, in die der Stempel drückt. So entsteht eine rohrförmige Welle, die länger ist als der ursprüngliche Massivrohling.
Gegenüber herkömmlichen Verfahren zur Herstellung von Hohlwellen spart das Bohrungsdrücken bis zu 80 Prozent der Kosten und die Hälfte des Materials. Mit dieser Art der Fertigung lassen sich außerdem gute Ergebnisse bei Materialien erbringen, die schwierig zu bearbeiten sind, etwa manche Stahlsorten oder bestimmte Legierungen. Außerdem empfiehlt sich Bohrungsdrücken bei sehr teuren Werkstoffen, da bei diesem Verfahren kaum Abfall anfällt.
Die erste Bohrungsdrückmaschine der Welt haben Wissenschaftler des Fraunhofer IWU und der Technischen Universität Chemnitz im DFG-Sonderforschungsbereich »Prozessketten der Massivumformung« entwickelt, gebaut wurde sie 1998 von der NILES-SIMMONS Industrieanlagen GmbH.