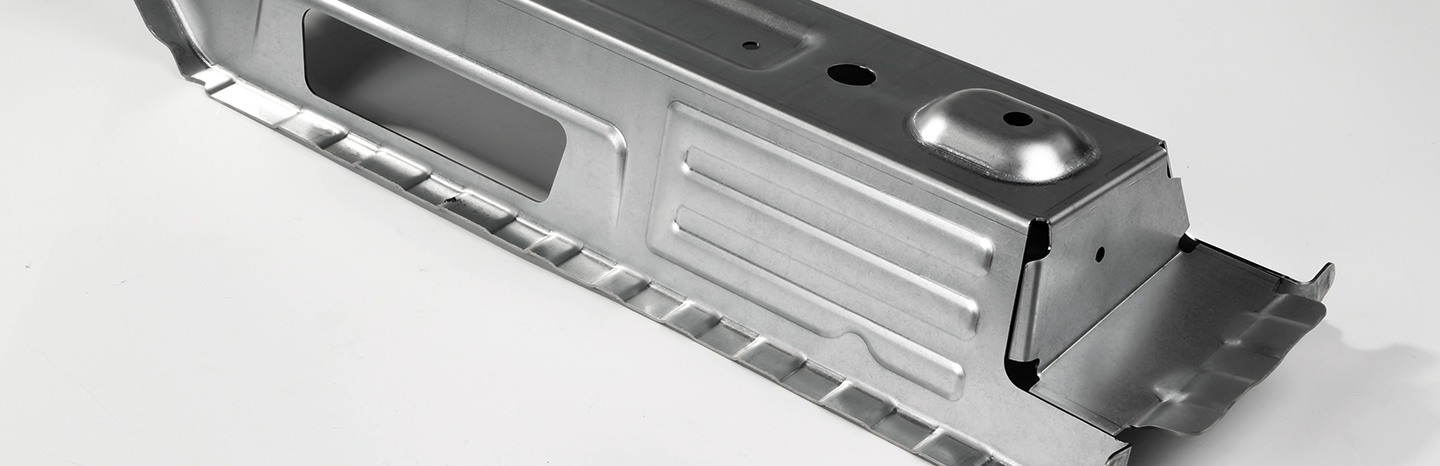
Umformwerkzeuge geben den vielen Blechbauteilen eines Autos ihre Form. Durch die zunehmende Vielfalt an Modellen auf dem heutigen Automobilmarkt wird dies zu einer wirtschaftlichen Herausforderung. Mit sinkenden Stückzahlen der Blechbauteile steigt der Anteil der Werkzeugkosten an den Herstellkosten der Blechbauteile. Das macht die Produktion der Komponenten mit herkömmlichen Verfahren und Prozessketten unwirtschaftlich.
Wie ein großer Teil der Werkzeugkosten gespart werden kann, wie man flexibler produziert und wie dabei gleichzeitig die Umwelt profitiert, zeigten die Wissenschaftler des Fraunhofer IWU im Rahmen der Innovationsallianz »Green Carbody Technologies« (InnoCaT®). Sie entwickelten eine neuartige Fertigungsmethode, bei der kleine Änderungen am Design des Bauteils große Effizienzsteigerungen bei seiner Herstellung ermöglichten.
Wie dies funktioniert, demonstrierten die Forscher anhand eines Sitzquerträgers. Konventionell wird dieses Teil in aufeinanderfolgenden Umformstufen durch Tiefziehen gefertigt. Bei dem neuen Verfahren gibt es lediglich einen einzigen bauteilspezifischen Umformschritt. Zunächst wird eine Blechplatine ausgeschnitten, die anschließend durch Formschlagen, der einzigen bauteilspezifischen Umformstufe, eine spezielle Struktur mit verschiedenen Vertiefungen erhält. Durch Abkanten wird das Bauteil dann in seine endgültige Form gebracht. Bei allen anderen Herstellungsschritten kommen flexible Fertigungstechniken auf CNC-Blechbearbeitungsmaschinen zum Einsatz. Um den Querträger so herzustellen zu können, wurde er geometrisch minimal angepasst. Über 90 Prozent der Geometrie sind identisch mit dem ursprünglichen Bauteil, sodass der Verbau im Karosseriebau sowie alle weiteren Fertigungsschritte nicht geändert werden müssen.
Dank der flexiblen Fertigung und der Reduzierung des Werkzeugaufwands um ca. 90 Prozent lässt sich je Bauteil eine deutliche Kostenersparnis erreichen. Bis zu einer Jahresstückzahl von 30 000 Stück kann so deutlich wirtschaftlicher und flexibler gefertigt werden als mit klassischem Tiefziehen. Durch den Entfall der Ankonstruktion für das Tiefziehen fällt die Platine kleiner aus und ermöglicht eine Reduzierung des Materialeinsatzes um 22 Prozent. Der Energieeinsatz für den Herstellungsprozess ließ sich um die Hälfte senken – ein wertvoller Beitrag zur Reduzierung des CO2-Ausstoßes.