Fraunhofer IWU und MOSOLF Special Vehicles GmbH
3D-gedruckte Regale für batterieelektrische Polizei-Einsatzfahrzeuge: damit möglichst viel Nutzlast erhalten bleibt
Batterieelektrische Fahrzeuge sind ein wesentlicher Beitrag zur CO2-Reduktion im Verkehrssektor. Das Mehrgewicht der Hochvoltspeicher geht jedoch auf Kosten der erlaubten Zuladung – es sei denn, das Fahrzeug wird an anderer Stelle leichter. Das Fraunhofer IWU und die MOSOLF Special Vehicles GmbH haben einen smarten Vorschlag, wie gleichzeitig Gewicht reduziert und dennoch der Bauraum optimal ausgenutzt werden könnte: durch ein 3D-gedrucktes Heckregal. Am Beispiel des Mercedes Vito lassen sich so im Vergleich zur bisherigen Nachrüstlösung einschließlich der Beschläge 26,5 Kilogramm einsparen.
Dabei bleibt die Nutzlast des Regalsystems vollständig erhalten. Auch im neuen Regal darf die untere Schublade mit bis zu 100 Kilogramm belastet werden. Belastbarkeit und flexible Nutzbarkeit des Systems sind wichtige Anforderungen, da die Ausrüstung für den Einsatz zunehmend schwerer wird. Ballistische (kugelsichere) Schutzschilde beispielsweise bringen einiges Gewicht auf die Waage. Dennoch muss die Nutzung im Verkehrsdienst, Streifendienst oder bei Großveranstaltungen als Mannschafttransport flexibel möglich sein. Das neu entwickelte Regal schmiegt sich vollständig an die Fahrzeughaut, erfordert keine zusätzlichen Versteifungen oder Befestigungen und nutzt so den Bauraum im Heckbereich bestmöglich aus. In den oberen Fächern finden sogar mehr Gegenstände Platz als bisher, dank einer um 8 Prozent vergrößerten Ablagefläche. Selbstverständlich ist das Regal auch genauso sicher wie die Standardausführung.
Für die Herstellung des neuen Regals kam die SEAM-Technologie zum Einsatz. SEAM steht für Screw Extrusion Additive Manufacturing. Dieses 3D-Druck-Verfahren eröffnet neue Produkt- und Fertigungsmöglichkeiten im industriellen Maßstab – es erlaubt, große Stückzahlen in kurzer Zeit zu wettbewerbsfähigen Kosten zu produzieren. Das am Fraunhofer IWU entwickelte SEAM-Verfahren ist im Vergleich zum herkömmlichen 3D-Druck nicht nur acht Mal schneller, sondern ermöglicht zudem die Verwendung preisgünstigen Standard-Kunststoffgranulats. Dadurch lassen sich im Vergleich zu klassischen Fused-Layer-Modeling (FLM)-Verfahren, in denen teures Filament verwendet wird, Materialkosten um das bis zu 200-fache einsparen. Beim neuen Heckregal fiel die Wahl auf ein kohlenfaserverstärktes, gegenüber Wasserkontakt unempfindliches Polypropylen (Akrolen® PP ICF 30).
Der Druckprozess erfolgt, indem über eine modifizierte Extrusionsschnecke das Kunststoffgranulat in den Extruder eingezogen und plastifiziert wird. Dabei können Prozessgeschwindigkeiten bis ein Meter pro Sekunde erreicht werden. Die entstehende Kunststoffschmelze wird anschließend schichtweise auf der Bauplattform abgelegt. Durch den kontinuierlichen Ablageprozess ist die Fertigung großvolumiger, belastbarer Bauteile möglich.
Die MOSOLF Special Vehicles GmbH gab den Anstoß für die Zusammenarbeit mit dem Fraunhofer IWU und brachte ihre Expertise zu Beladung, Konzept, montagegerechter Gestaltung, Musterbau und Anbindung im Fahrzeug ein. Die Partner wollten den Beweis antreten, dass 3D-gedruckte Innenausbauten bei vergleichbaren Herstellkosten technische Vorteile gegenüber herkömmlichen Lösungen bieten. Beweis erbracht: Das SEAM-Verfahren ist eine wirtschaftliche Option für fahrzeugtyp-spezifische sowie an individuelle Kundenanforderungen angepasste Kleinserien.
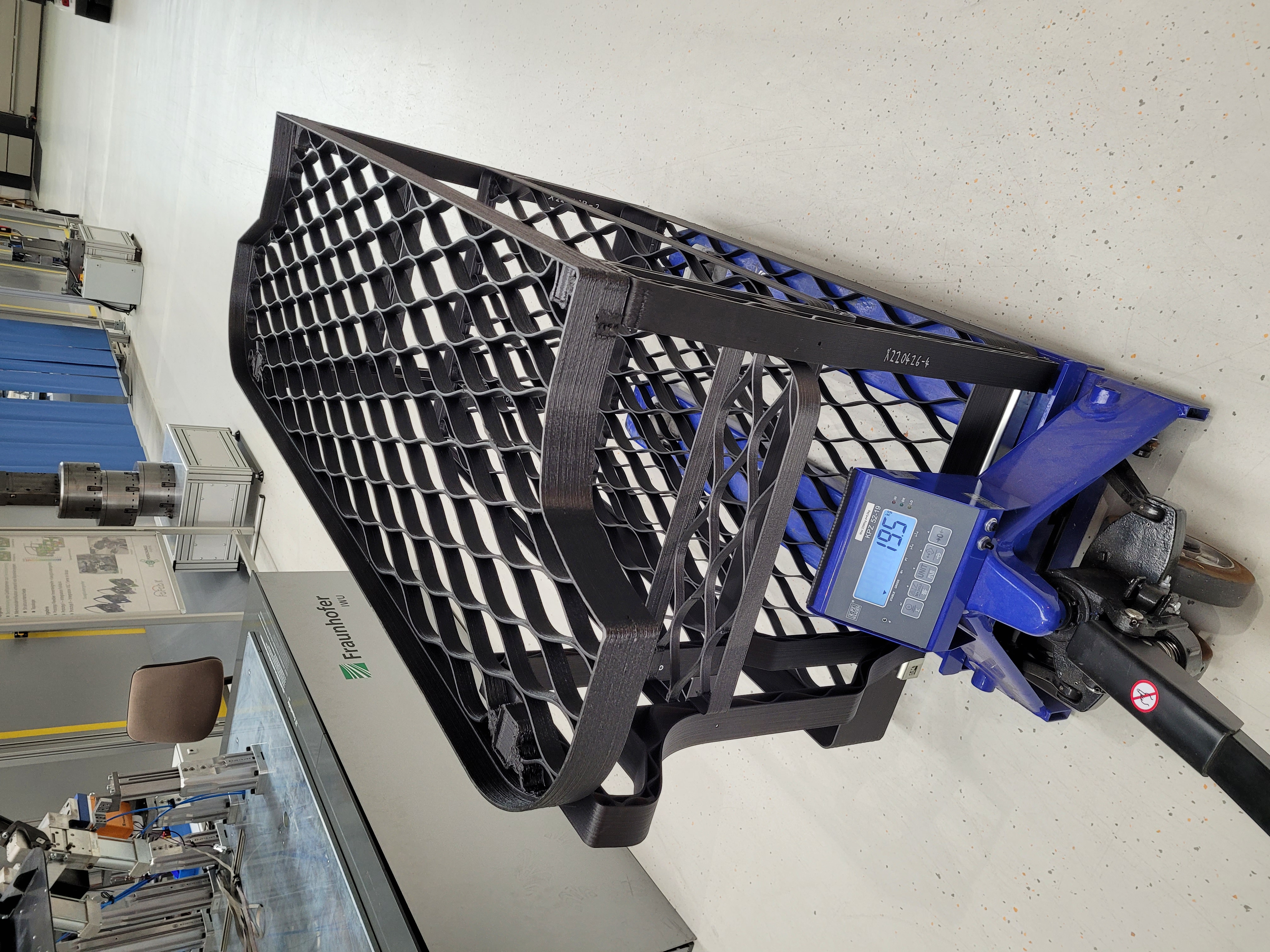
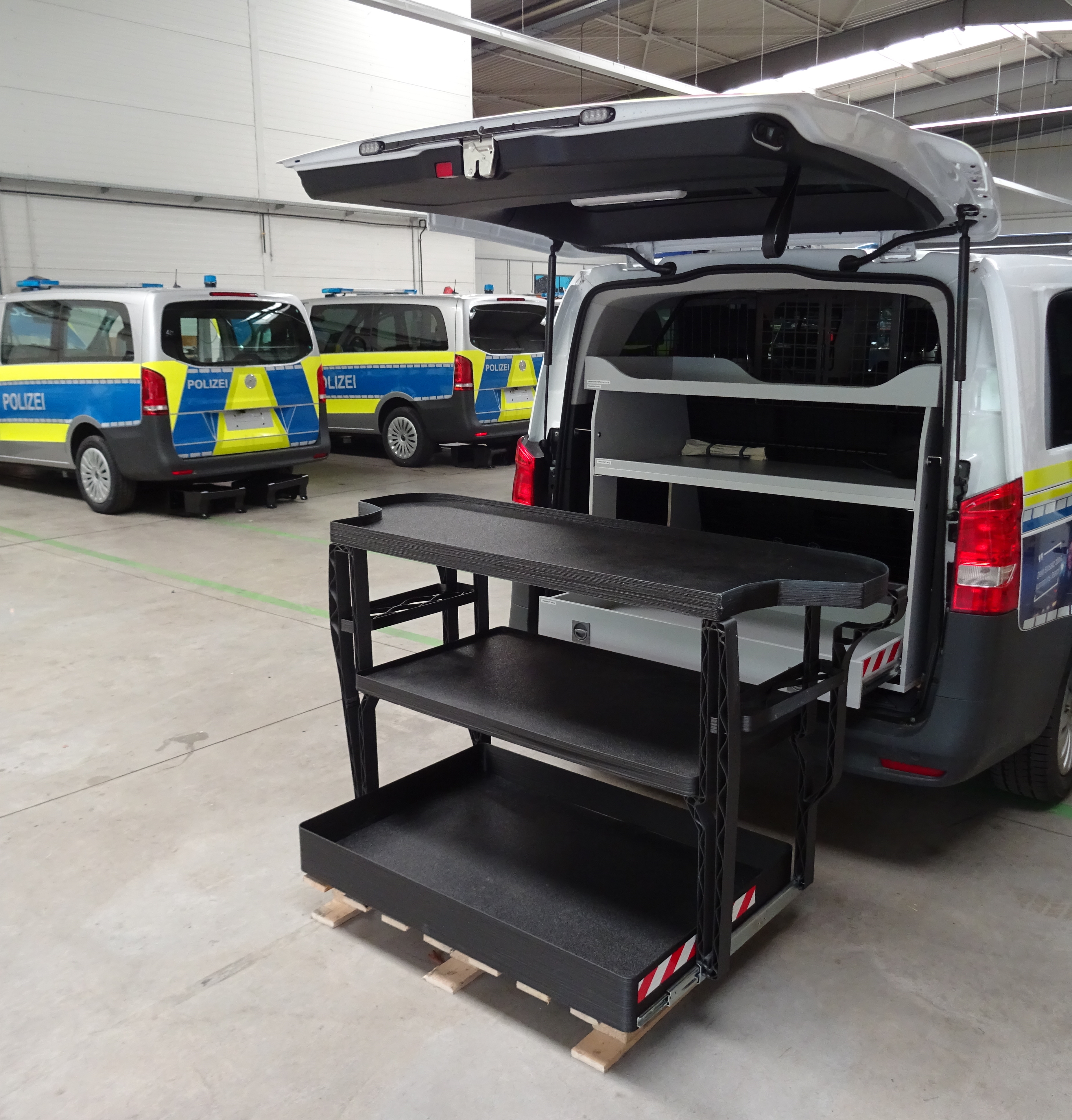
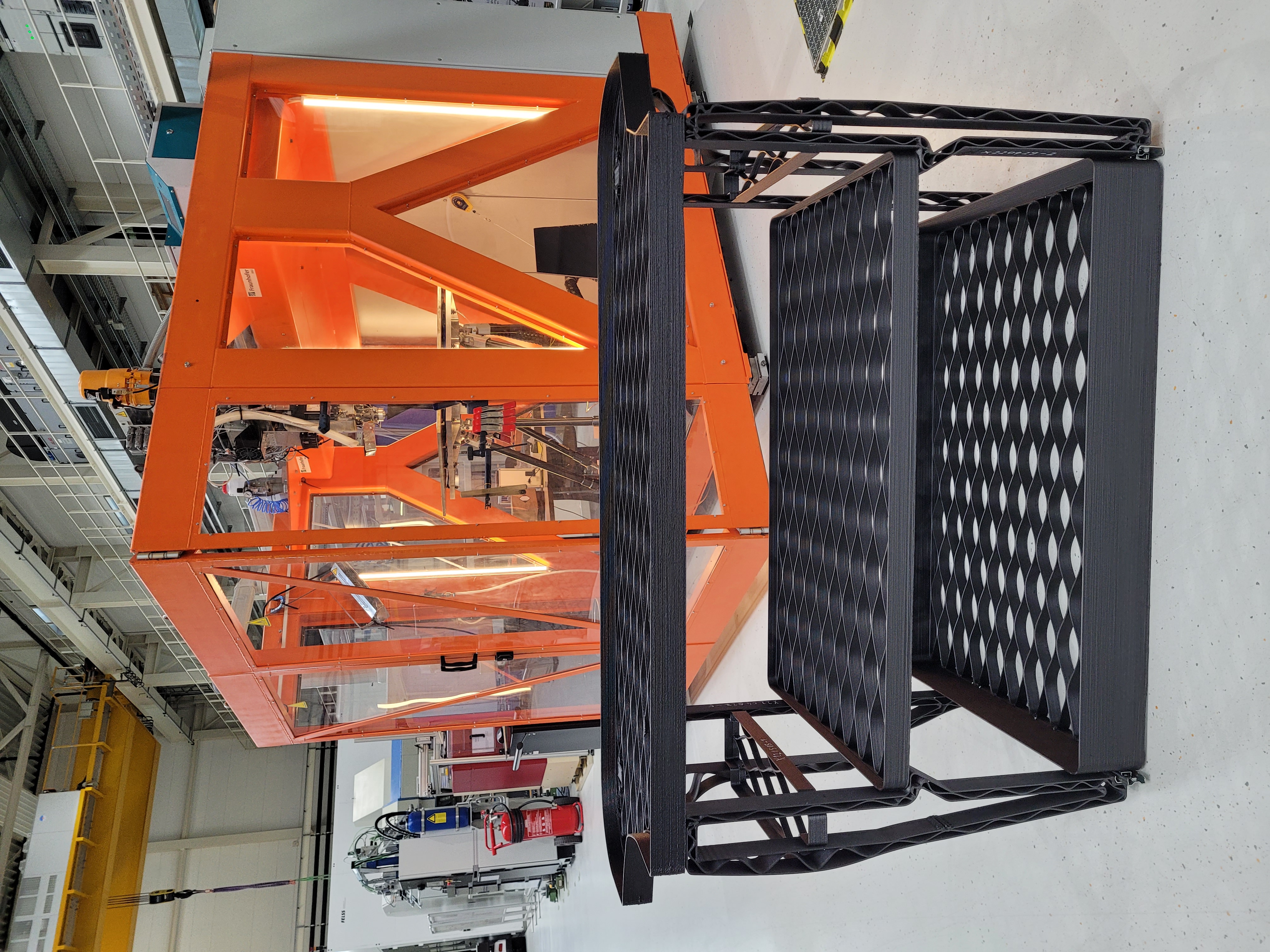