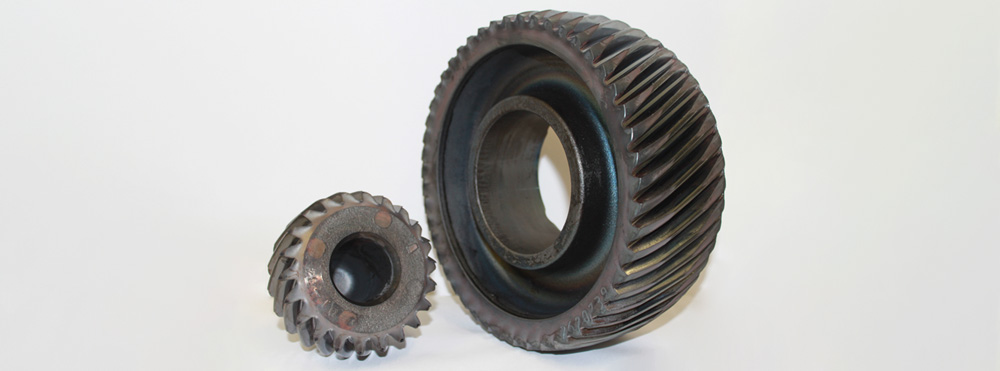
Das Fraunhofer IWU hat in den vergangenen zwanzig Jahren ein umfangreiches Know-how auf dem Gebiet des Kaltwalzens von getriebetypischen Pkw-Laufverzahnungen ins volle Material aufgebaut. Bei gleichzeitiger Nutzung der Vorteile der Warmumformung konnte dem Verzahnungswalzen die Chance auf ein industriell interessantes Teilesortiment in Form von großmoduligeren Bauteilen aus dem Nutzfahrzeugsektor erschlossen werden.
Das Projekt »Warmwalzen von Schrägverzahnungen auf präzisionsgeschmiedete Halbzeuge (WWSV)« hatte das Ziel, durch eine innovative Fertigungsfolge sowohl für Losräder als auch für wellen- bzw. zapfenförmige Getriebebauteile signifikante Materialeinsparungen gegenüber spanend gefertigten Verzahnungen nachzuweisen.
Im Ergebnis wurden erstmals Schrägverzahnungen mit einer Zahnhöhe von hz = 9 mm durch Warmquerwalzen auf präzisionsgeschmiedete Bauteile als Vorverzahnungsprozess (Weichbearbeitung) hergestellt.
An diesen Demonstratoren D1 (Welle; mn = 4 mm; z = 22) und D2 (Losrad; mn = 4 mm; z = 49) erfolgten anschließend weitere Untersuchungen. So wurde am Demonstrator D1 die Zahnfußtragfähigkeit nach der Wärmebehandlung und dem Schleifen untersucht, in deren Ergebnis eine um 14%-höhere Tragfähigkeit an warmgewalzten im Vergleich zu gefrästen Zahnrädern bei bearbeitetem Zahngrund ermittelt wurde.
Am Demonstrator D2 (mn = 4 mm / z = 49) wurden die Potenziale hinsichtlich des parallelen Einsatzes von Antioxidationsmittel und Schmierstoff ermittelt. Die maximale Prozesskraft konnte mittels Minimalmengenschmierung um 15%, die Momentenauslastung der Walzspindeln mittels Minimalmengenschmierung sowie werkstückseitiger Vorbehandlung mit Antioxidationsmittel um 18% reduziert werden. Mit beiden Prozessoptimierungen ließ sich nur eine marginale Oberflächenverbesserung feststellen.
Ergebnisse
Infolge der geringeren Durchmesserdimensionen von Walz- gegenüber Frästeilvorformen konnten bei beiden Demonstratoren signifikante Materialeinsparungen nachgewiesen werden. Das würde für die beteiligten Schmiedeunternehmen folgende Einsparpotenziale mit sich bringen:
Laufzeit
März 2021 bis August 2023
Projektpartner
Das IGF-Vorhaben 21698 BR der Forschungsvereinigung Forschungsgesellschaft Stahlverformung e.V. wurde über die AiF im Rahmen des Programms zur Förderung der Industriellen Gemeinschaftsforschung (IGF) vom Bundesministerium für Wirtschaft und Klimaschutz (BMWK) aufgrund eines Beschlusses des Deutschen Bundestages gefördert.