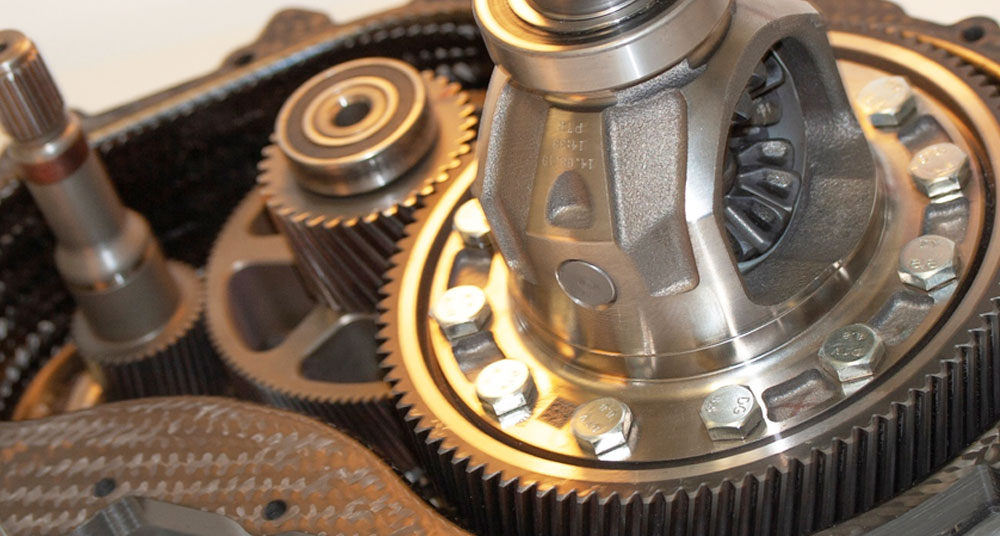
Herausforderung
Im Kontext knapper werdender Ressourcen und wachsendem Bewusstsein für den globalen Klimaschutz rückt der E-Antrieb als die zukünftige Mobilitätslösung in den Fokus aktueller Entwicklungen. Durch die politischen Forderungen und verstärkte öffentliche CO2-Diskussion bezüglich lokalem Ausstoß im urbanen Umfeld erschließen nun auch klassische Hersteller mit neu entwickelten E-Fahrzeugen, versorgt von Batterien und teils auch von Brennstoffzellen, den Markt.
Das Getriebe als leistungsübertragende Komponente des Antriebstrangs zur Anpassung von Drehmoment und Drehzahl kommt heutzutage in fast allen Fahrzeugen zum Einsatz und wurde seit Jahrzehnten stetig optimiert. Für den Einsatz in modernen E-Antrieben ändern sich jedoch auch die Anforderungen an die nun von Elektromotoren gespeisten Getriebe. Dabei steht der Aspekt der Senkung der Umweltbelastung im klaren Fokus.
Lösung
Bestehende Ansätze neu kombiniert.
Wichtige Kriterien eines neuen ganzheitlichen Ansatzes sind ein nahezu wartungsfreier Langzeitbetrieb, die Reichweitenerhöhung durch Wirkungsgradoptimierung und Leichtbau, weniger Spanvolumen durch Verzahnungswalzen sowie eine möglichst maximal ressourceneffiziente Gesamtproduktionskette in der E-Antriebsfertigung. Ein Zielkonflikt besteht diesbezüglich zwischen Leichtbau und Akustik, was zukünftig mit einem neuen Ansatz zur strukturellen Trennung des Getriebegehäuses gelöst werden soll.
Zur Bearbeitung des Projekts wurde auf eine enge Verknüpfung der Kompetenzen in den Bereichen Verzahnungs- und Getriebetechnik (Fraunhofer IWU), Oberflächentechnik (Fraunhofer IWS) und Leichtbautechnologien (Fraunhofer ICT) gesetzt. Der Schlüssel zum Erfolg war die Zusammenführung bzw. Kombination der walztechnischen Herstellung von Verzahnungen, versehen mit einer superharten amorphen Kohlenstoffbeschichtung, die im Idealfall einen schmiermittelfreien Betrieb bei sehr hohem Wirkungsgrad erlaubt.