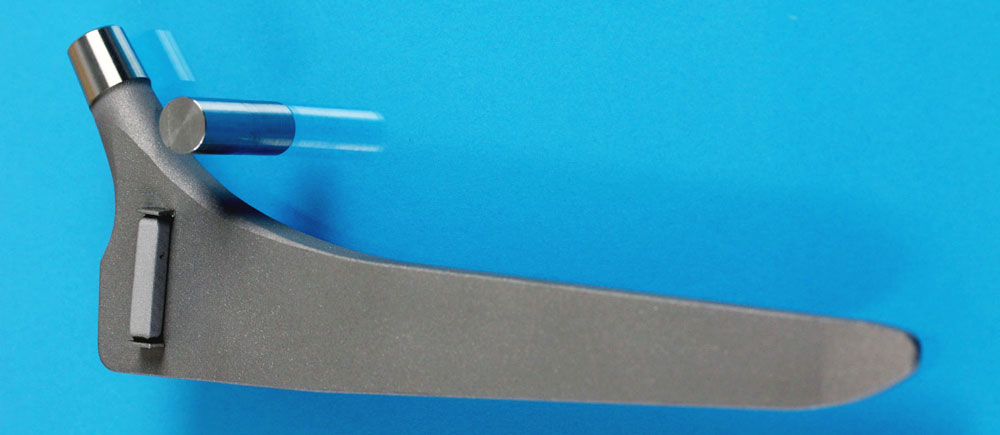
Neue Fertigungstechnologien
Im Fraunhofer-Leitprojekt Theranostische Implantate haben sich zwölf Fraunhofer-Institute zusammengeschlossen, um Implantate zu entwickeln, die Dysfunktionen detektieren und Gegenmaßnahmen initiieren. Im Projekt entsteht u.a. der Demonstrator »Smarte Hüftgelenkprothese«. Aufbauend auf dem adaptiven Prothesensystem entwickeln die Wissenschaftler des Fraunhofer IWU gemeinsam mit den Partnerinstituten eine Hüftprothese, die mit Sensoren und Aktoren ausgestattet ist. Sie erlaubt es, ihr Einwachsverhalten und ihren Sitz im Knochen ohne invasiven Eingriff laufend zu überwachen und bei Bedarf nachzujustieren.
Um das theranostische Hüftimplantat technisch zu realisieren, konzentriert sich das Fraunhofer IWU auf die Entwicklung neuer Fertigungsprozesse bzw. auf die Entwicklung hybrider Fertigungstechnologien. Das Ziel der Wissenschaftler ist es, Sensoren und Aktoren zu integrieren, ohne dabei die Komponenten zu beschädigen oder die mechanischen Eigenschaften der Implantate im Vergleich zu kommerziellen Systemen negativ zu beeinflussen. Der Schlüssel dazu ist die Kombination von Verfahren aus den Bereichen der Umformung, der generativen Fertigung, der Zerspanung und des thermischen Fügens.
Eine der Lösungen ist die Integration des Sensor-Aktor-Systems in geschmiedete Komponenten. Dabei erhalten die Implantatgrundkörper Öffnungen und Taschengeometrien, in die sich die zusätzlichen Komponenten integrieren lassen. Diese Grundkörper können anschließend per Laserschweißen thermisch gefügt werden. Umfangreiche simulative und experimentelle Untersuchungen bestätigen, dass die so gefertigten Bauteile den nötigen, hohen mechanischen Anforderungen genügen.
Die Umformtechnik bietet ebenfalls großes Potenzial bei der Nachverfestigung generativ gefertigter Komponenten. Dieses Finishing ist essenziell bei Titanbauteilen, die mittels Laserstrahlschmelzen hergestellt wurden. Neben einer Wärmebehandlung unter Schutzgas, dem heiß-isostatischen Pressen, zeigt auch das Nachschmieden sehr gute Ergebnisse. Besonders interessant ist dabei die selektive Nachbearbeitung der mechanisch am höchsten beanspruchten Bereiche der intelligenten Prothese.
Als weitere Fertigungsvariante wurde in Zusammenarbeit mit dem Fraunhofer IKTS ein Integrationskonzept auf Basis des Laserstrahlschmelzens entwickelt. Das Metallpulver wird dazu schichtweise und lokal im Bereich der Laserbearbeitungszone aufgeschmolzen. Dabei wird ein Aktor auf Basis eines keramischen Mehrschichtsystems während der generativen Fertigung des Hüftimplantats integriert. Das System ist hermetisch im Titanimplantat verkapselt und kann berührungslos von außerhalb des Körpers angesteuert werden, um es definiert zum Schwingen anzuregen. Eine Veränderung der Implantat-Knochen-Schnittstelle resultiert dabei auch in Veränderungen der dynamischen Eigenschaften des Implantat-Knochen-Verbundes. Das heißt, ein zu lockerer Implantat-Knochen-Verbund schwingt anders als ein perfekt sitzender. Dass die dafür nötige Energieübertragung von außen funktioniert, belegen umfassende experimentelle Untersuchungen.
Die neu entwickelten Aktoren lassen sich durch ihre Modulbauweise auch in andere Implantatsysteme integrieren und sind eine Möglichkeit zur Überwachung der Implantat-Knochen-Schnittstelle sowie zum Conditon Monitoring komplexer Bauteile.