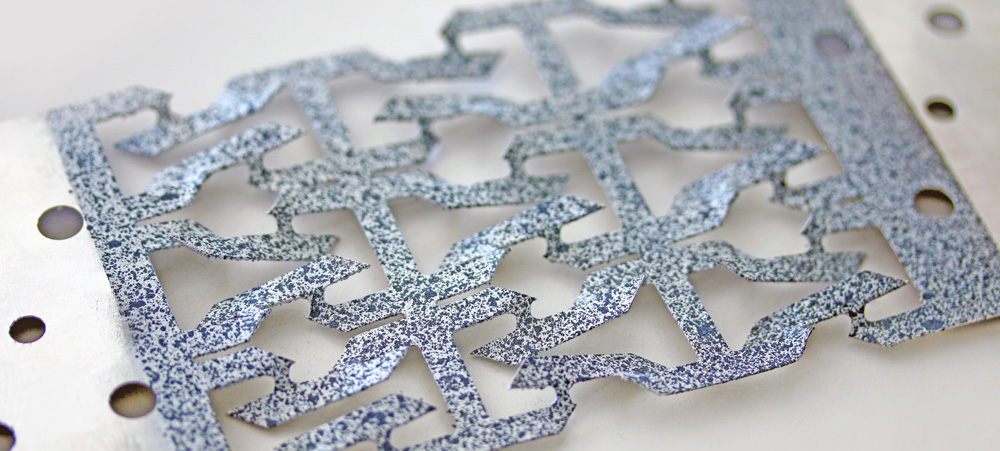
Herausforderung
Faser-Kunststoff-Verbunde (FKV) sind aufgrund ihrer hohen spezifischen Steifigkeiten und Festigkeiten bevorzugte Leichtbauwerkstoffe. Ein Defizit besteht derzeit noch in der unzureichenden Energieabsorption im Versagensfall. Verbesserungen in der Crashperformance lassen sich z. B. durch die gezielte Verstärkung der FKV-Struktur mit duktilen, metallischen Einlegern erzielen. Am Fraunhofer IWU wurde ein innovativer, mehrskaliger Umformprozess entwickelt, mit dem derartige Hybridbauteile effizient und eigenschaftsoptimiert hergestellt werden können.
Lösung
Bei konventionellen Konzepten werden das FKV-Bauteil und die metallische Komponente in der Regel separat gefertigt und in einem nachfolgenden Prozessschritt, der Hybridisierung, zum Hybridbauteil gefügt. Zur signifikanten Verkürzung der Prozesskette wurde am Fraunhofer IWU im Rahmen des DFG-Schwerpunktprogramms »SPP1712 – intrinsische Hybridverbunde« ein mehrskaliger Umformprozess entwickelt. Bei diesem Umformprozess werden die drei bisher sequentiell ablaufenden Prozessschritte – die Erzeugung der makroskopischen Bauteilgeometrie, die Hybridisierung und die Herstellung von mesoskopischen Formschlusselementen – in einem Prozessschritt zusammengefasst. Um den intrinsischen Prozess zu realisieren, wurde ein spezieller metallischer Einleger entwickelt. Dieser wird als zunächst noch ebene Struktur zwischen die FKV-Lagen eingebracht. Während der makroskopischen Formgebung wird der Einleger zusätzlich auf Zug beansprucht. Durch die simulativ ausgelegte Geometrie werden in Folge der Zugbeanspruchung mesoskopische, aus der Blechebene hervortretende Formschlusselemente ausgebildet. Während der makroskopischen Formgebung werden sie in den umgebenden FKV eingeformt und erzeugen eine formschlüssige, in Teilen sogar hinterschnittige Verbindung zwischen dem Einleger und den Faserfilamenten. Dadurch wird die Kraft- und Schubübertragung zwischen dem Einleger und dem FKV erheblich verbessert und ein strukturmechanisch günstiger, gradierter Übergang erzeugt. Als Demonstratorbauteil wurde eine Schwellergeometrie ausgewählt. Neben der simulativen Auslegung des Umformprozesses wurde auch das entsprechende variotherme Umformwerkzeug am Fraunhofer IWU entwickelt. Durch den Einsatz dieses innovativen, mehrskaligen Umformprozesses sind sowohl eine Effizienzsteigerung bei der Herstellung von Hybridbauteilen als auch signifikante Verbesserungen der statischen und dynamischen Bauteilperformance zu erwarten. Dies ist auf die mechanische Verklammerung und damit formschlüssige Anbindung zwischen FKV und Metall zurückzuführen. Damit steht ein Prozess zur Verfügung, mit dem hochbelastbare Hybridbauteile energie- und kosteneffizient in nur einem Prozessschritt gefertigt werden können.