Blechexpo
Lösungen für stückzahlflexible Fertigung und mobile Bearbeitung
Auch 2019 ist das Fraunhofer IWU auf der internationalen Fachmesse für Blechbearbeitung Blechexpo in Stuttgart vom 5. bis 8. November vertreten. Auf dem Fraunhofer-Gemeinschaftsstand in Halle 3, Stand 3241 zeigen die Forscher am Beispiel des Konzeptfahrzeugs Silberhummel®, wie man die wirtschaftliche Produktion kleinster Stückzahlen realisiert. Zudem wird eine mobile Bearbeitungsmaschine vorgestellt, mit der komplexe Großbauteile wesentlich kostengünstiger und zeitsparender bearbeitet werden können. Darüber hinaus präsentiert sich das Fraunhofer IWU bei seinem Projektpartner Anchor Lamina in Halle 4, Stand 4212 mit einem intelligenten Gleitlagerversuchsstand.
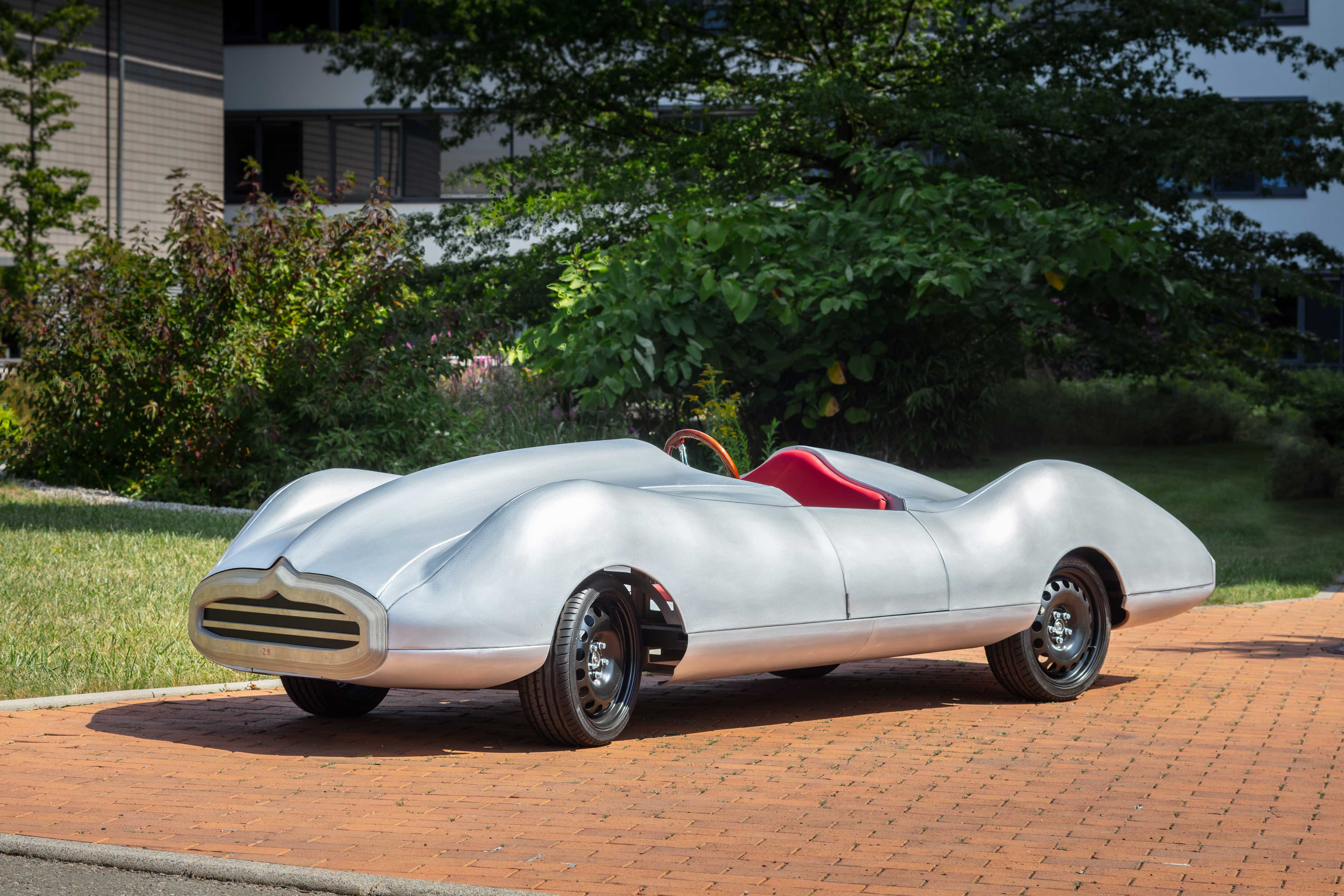
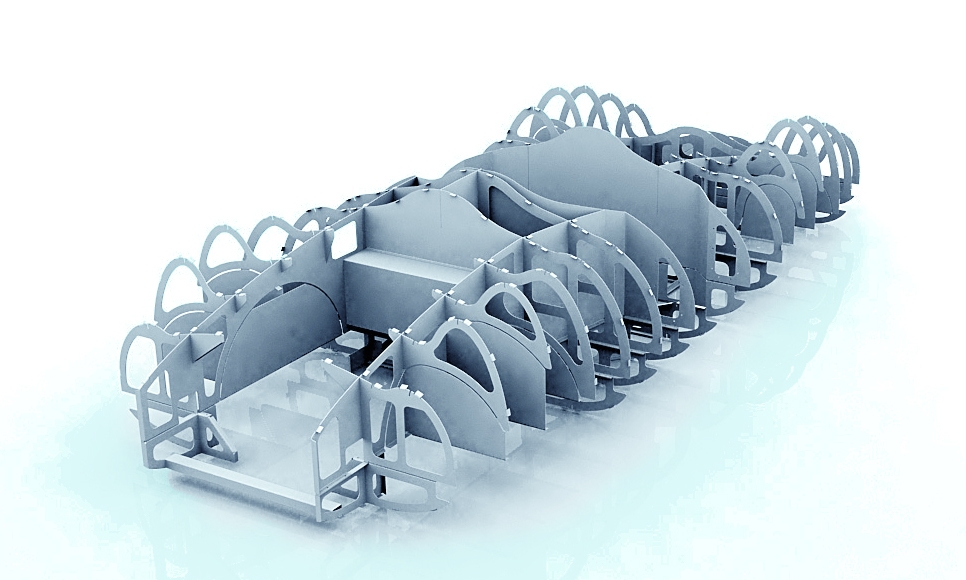
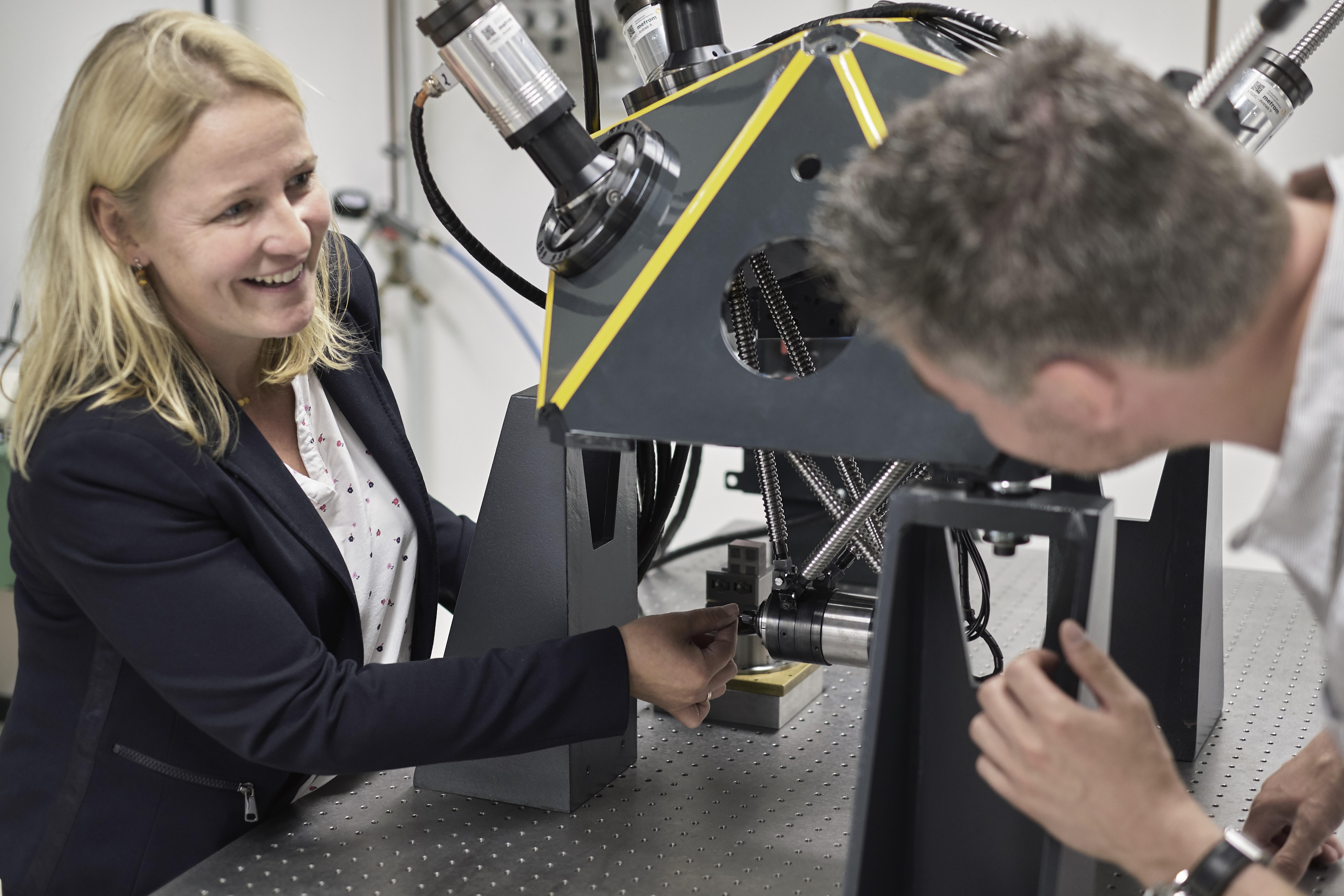
Automobilproduktion in Stückzahl 1
Der Trend zur Individualisierung industriell hergestellter Produkte macht auch vor dem Automobilbau nicht Halt. Eine industrielle Automobilproduktion in Stückzahl 1 scheint jedoch auf den ersten Blick nicht möglich, wenn man bedenkt, dass ein einzelnes Umformwerkzeug für ein Karosseriebauteil hunderttausende Euro kosten kann. Und da eine Karosse aus vielen verschiedenen Bauteile besteht, kann man schnell nachvollziehen, dass ein konventionell produzierter Wagenaufbau unbezahlbar ist. Das Fraunhofer IWU hat nun einen Verfahrensmix entwickelt, mit dem die Produktion auch für Unikate wirtschaftlich möglich ist - und das nicht nur im Automobilbau.
Mit dem Technologiedemonstrator Silberhummel® präsentiert das Fraunhofer IWU technologisch verschieden geformte Bauteile vereint an einem Objekt. Die Silberhummel® – ein stromlinienförmiges Konzeptfahrzeug – basiert auf Plänen eines nie gefertigten Rennwagens des Automobilherstellers Auto Union. Ein Forscherteam des Instituts rekonstruierte das Fahrzeug und fertigte die Außenteile des Modells. Die Karosserie besteht aus Benchmark-Teilen, die mit verschiedenen am Institut entwickelten Umform-, Füge- und generativen Fertigungstechnologien für kleine und kleinste Stückzahlen hergestellt wurden.
Die komplexen Außenhaut-Bauteile der Silberhummel® wurden per inkrementeller Blechumformung gefertigt – einem Verfahren, das sich bereits ab Stückzahl 1 rechnet. Im Vergleich zu konventionellen Ziehverfahren kann dabei auf aufwendige Werkzeuge verzichtet werden. Dadurch reduzieren sich die Werkzeugkosten und die Zeit bis zum ersten Fertigteil. Für das Verfahren wird lediglich eine Gegenform aus Holz benötigt – in diesem Fall wurde kostengünstiges und leicht zu bearbeitendes Leimholz verwendet. Aus dem Holz, das als Quader in den Dimensionen eines Esstisches angeliefert wird, fräst ein Bearbeitungszentrum am Institut die Form der Kotflügel, der Motorabdeckung oder der Seitenteile heraus. Im Vergleich zu konventionellen Werkzeugen benötigt dieser Prozess nur ein Drittel der Zeit. Anschließend wird das Werkzeug in ein speziell angepasstes Portalbearbeitungszentrum montiert und das passende Blech in einen Rahmen über dem Werkzeug gespannt. Ein halbkugelförmiger Drückdorn, der anstelle des Bohr- oder Fräskopfes im Großbearbeitungszentrum sitzt, fährt Bahn für Bahn über das Blech und drückt es gegen die Patrize, bis es seine endgültige Form angenommen hat.
Nun werden die so entstandenen Außenhaut-Komponenten auf eine Tragkonstruktion aus Blechspanten aufgebracht. Die Spanten wurden mit einem weiteren hochflexiblen Verfahren hergestellt, dem Stanzen-Biegen-Fügen, kurz StaBiFü®. Der StaBiFü®-Ansatz wurde als wirtschaftliche Alternative zu mehrstufigen Umformprozessen am Fraunhofer IWU entwickelt. Kern des Ansatzes ist es, den bauteilspezifischen Formspeichergrad in Folgeverbundwerkzeugen signifikant zu reduzieren. Minimiert auf eine einzige bauteilspezifische Umformstufe können bis zu 90 Prozent der Werkzeugkosten eingespart werden und auch wenige Blechteile wirtschaftlich hergestellt werden.
Nach Anfertigung der einzelnen Komponenten werden diese zu einer ganzen Karosserie verbunden. Das Schweißen geschieht nicht wie üblich robotergesteuert und unter Schutzgasatmosphäre, sondern vorrichtungsfrei und manuell durch scannerbasierte Laserhandgeräte. Mit diesem Mix an neuartigen, schnellen und flexiblen Herstellungsprozessen vergingen von der Idee bis zur fertigen Karosserie der Silberhummel® nur wenige Monate.
Die Maschine kommt zum Werkstück
Wenn Großbauteile, wie sie z. B. im Bereich der Energietechnik, des Werkzeug- und Anlagenbaus oder auch des Flugzeugbaus eingesetzt werden, einer Nachbearbeitung unterzogen werden müssen, ist dies für den Anlagenbetreiber oft mit hohen Kosten und Risiken verbunden. Das resultiert aber nicht nur aus der Stillstandzeit der Anlage; ein anderer Grund ist der schwierige und teure Transport der Bauteile hin zu spezialisierten Unternehmen, wo sie auf Großbearbeitungszentren ausgebessert werden.
Ein wirtschaftliches Risiko, wenn man bedenkt, dass die an den Großbauteilen zu bearbeitenden Bereiche oft nur auf einen lokalen Bereich beschränkt sind. Wesentlich effizienter und kostengünstiger ist die Lösung, die nun ein Team von Wissenschaftlern des Fraunhofer IWU und der METROM Mechatronische Maschinen GmbH entwickelt hat: eine mobile Bearbeitungsmaschine, die sozusagen direkt zum Werkstück kommt und am zu bearbeitenden Bereich positioniert wird. Die 5-Achs-Werkzeugmaschine besteht aus nur wenigen Baugruppen und kann daher zügig zum Kunden gebracht und dort einsatzbereit zusammengebaut werden. Die fünf Achsen ermöglichen eine exakte Ausrichtung zum zu bearbeitenden Werkstück im Bearbeitungsraum. Da die Bearbeitung von oben erfolgt, ist eine Bewegung des Bauteils von unten nicht nötig. Einen weiteren Vorteil bieten die integrierten Zusatzfunktionen: Neben verschiedenen Fräsprozessen gelingt es mit der Parallelkinematik, auch Fertigungsverfahren wie bspw. Lichtbogen-Auftragsschweißen oder Laser-Pulver-Auftragsschweißen durchzuführen.
Die Kostenvorteile für den Anlagenbetreiber liegen auf der Hand: Nicht nur der riskante Transport dieser investitionsintensiven Großbauteile entfällt, auch die Ausfallzeiten der Anlage werden gesenkt, wie das Beispiel einer Turbinenreparatur zeigt. Der Reparatureinsatz einer Turbine dauert im Normalfall 3 bis 4 Wochen. Mit der mobilen 5-Achs-Werkzeugmaschine braucht es nur wenige Tage. Allein für das Einmessen des Bauteils werden nur wenige Minuten benötigt. Das spart den Kunden viel Zeit und Geld.
Effizientes Finishing mit piezoelektrischem Oberflächenhämmern
Eine mögliche Anwendung der mobilen Maschine – das piezoelektrische Oberflächenhämmern – präsentieren die Fraunhofer-Forscher ebenfalls auf dem Gemeinschaftsstand. Beim Oberflächenhämmern (OFH) handelt es sich um ein inkrementelles Umformverfahren, das vor allem im Werkzeug- und Formenbau zum Glätten, Verfestigen und Verdichten von Oberflächen eingesetzt wird. Dies geschieht, indem ein kugelförmiges Werkzeug, der sogenannte Hammerkopf, kontinuierlich auf die zu bearbeitende Werkstückoberfläche schlägt. Das OFH wird bereits seit vielen Jahren zur Endbearbeitung von z. B. Umform- und Spritzgießwerkzeugen, 3D-gedruckten/gesinterten Bauteilen, Gleitlagern oder Turbinenschaufeln verwendet.
Dass dieses Finishing-Verfahren noch wesentlich produktiver gestaltet werden kann, beweisen die Forscher des Fraunhofer IWU anhand eines piezogetriebenen OFH-Werkzeugs. Während das konventionelle OFH mit pneumatischen oder elektromagnetischen Aktoren arbeitet, kommt bei der Neuentwicklung ein piezoelektrischer Aktor zum Einsatz. Im Vergleich zu konventionellen OFH-Werkzeugen, die mit Hämmerfrequenzen zwischen 200 bis 500 Hertz arbeiten, werden mit diesen piezoelektrisch betriebenen OFH-Werkzeugen Hämmerfrequenzen von mehr als 1000 Hertz erreicht. Damit verbunden ist eine Produktivitätssteigerung um mindestens 50 Prozent. Ein weiterer Vorteil der piezoelektrischen Antriebseinheit liegt darin, dass die Prozessparameter automatisiert identifiziert und überwacht werden können. So kann das Verfahren robuster gestaltet und die Wirtschaftlichkeit erhöht werden. Geplant ist die Anwendung des Verfahrens auf Industrierobotern, wodurch – im Vergleich zum Einsatz klassischer Großbearbeitungszentren – eine Senkung der Maschinenstundensätze erreicht werden kann.
Intelligentes Hybridgleitlager
In Umformpressen üblicherweise verbaute Gleitlager unterliegen starken Belastungen: Zum einen werden sie durch die Vorspannung bereits im Ruhezustand der Presse belastet, zum anderen durch die Stößelbewegungen beim Umformvorgang selbst. Ein schadhaftes Gleitlager führt zum Maschinenausfall und kostenintensiven Stillstandzeiten.
Im Rahmen einer Forschungspartnerschaft zwischen dem Fraunhofer IWU, der Anchor Lamina GmbH sowie dem Institut für Tribologie und Energiewandlungsmaschinen der TU Clausthal im Rahmen eines VDW-Forschungsprojektes wurde ein Betriebskonzept entwickelt, mit dem Schäden an konventionellen Gleitlagern vermieden werden können. Eine Sensorik im Gleitlager - genauer gesagt sind an zwölf Punkten Sensoren angebracht - detektiert den aktuellen Belastungszustand und gleicht diesen mit Daten ab, die zuvor in Simulationen ermittelt wurden. Dadurch wird frühzeitig erkannt, ob ein kritischer Betriebszustand einzutreten droht. Ist dies der Fall, wird automatisch ein hydrostatisches Gleitlager zeitweise zugeschaltet.
Das intelligente Hybridgleitlager wurde bereits auf TRL4-Niveau getestet und ermöglicht neben dem sicheren Pressenbetrieb bei geringen Drehzahlen u. a. auch einen temporären Lagerstillstand und das Anlaufen unter Last - beides Betriebsarten, die das Einsatzpotenzial mechanischer Servopressen deutlich erweitern. Präsentiert wird es auf dem Messestand der Anchor Lamina GmbH in Halle 4, Stand 4212.