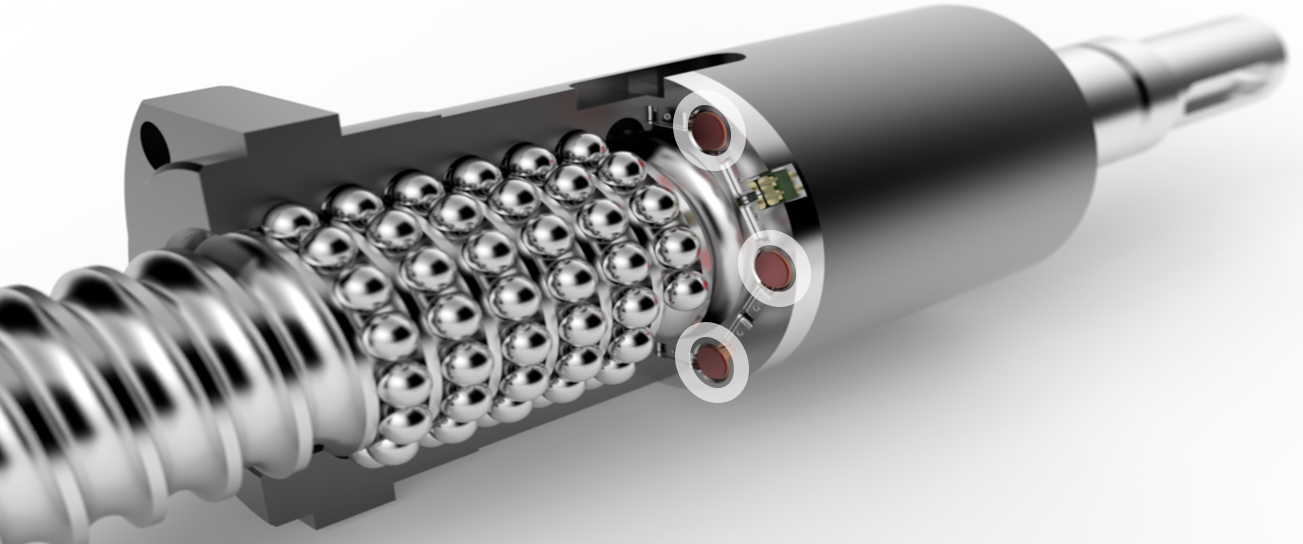
Actuators are key elements in practically every production plant and machine.
In many potential applications, such as adaptive bearing preload or wear compensation in cutting tools, there is currently no space to achieve the required forces, travel ranges and accuracies. For this reason, actuators based on thermal shape memory alloys (SMA) should be used where the space is too small for conventional actuators (e.g. piezo, pneumatic or hydraulic actuators).
In comparison, SMAs have the highest energy density and thus can achieve the required forces (> 1 kN) and travel ranges (<1 mm) with high precision in significantly smaller installation spaces. However, due to the thermal activation, a challenge with shape memory actuators lies in the dynamics (especially when cooling down) of the switching processes. In the project HochPerForm, developed by Fraunhofer IWU together with Fraunhofer IPM and IFAM, the cooling process is to be accelerated by a factor of 100 using switchable heat pipes. Thus, the working frequencies can be increased to over 1 Hz. In connection with the achievable travel ranges and forces, these performance parameters are unique and cannot currently be achieved with any other actuator technology. For further miniaturization, generative manufacturing processes are used, which are intended to enable optimal use of the available installation space. The application scenario is an adaptive bearing in a ball screw of a machine tool.