Zielbranche
Druckgussbranche, Werkzeugfertigung
Problemstellung
Neue Motorenkonzepte versprechen Verbesserungen in Drehmoment, Leistung und Wirkungsgrad – Fortschritte, die zu hohen thermomechanischen Beanspruchungen speziell der Leichtbaukomponenten führen. Für die Druckgussbranche ist dieser Trend eine Herausforderung, da komplizierte Druckgussteile oft nur mit Nachteilen in Qualität und Kosten hergestellt werden können. Um die Wirtschaftlichkeit zu erhöhen, müssen neue Wege im Entwicklungs- und Fertigungsprozess eingeschlagen werden.
Hochleistungsmotoren unterliegen massiven thermischen und mechanischen Beanspruchungen. Im Premium-Segment der Motorenklassen bringt die AUDI AG mit dem neuen 4.0l-V8-TFSI-Motor ein umweltfreundliches Hochleistungsaggregat auf den Markt. Der Grundmotor besteht aus dem Zylinderkurbelgehäuse und einer unterhalb angelagerten Lagertraverse. Diese wird aus einer Aluminiumlegierung im Druckgießverfahren hergestellt. Dabei können lokale Gas- und Erstarrungsporositäten auftreten, welche die Bauteilqualiät wesentlich beeinträchtigen.
Lösung
Diese Porositäten müssen unbedingt minimiert bzw. vermieden werden, um die statischen und dynamischen Festigkeiten zu garantieren sowie die Bauteildichtheit sicherzustellen. Als besonders kritisch erweist sich die Geometrie des Ölfiltertopfes der Lagertraverse. In diesem Bereich treffen hohe Funktionsanforderungen des Bauteils und besonders schwierige gießtechnische Bedingungen aufeinander. Eine Methode zur Reduktion der Porositätsvolumina ist das Einbringen einer zusätzlichen Temperierung im Bereich des Ölfiltertopfes. Hier stoßen jedoch auch modernste Methoden der Werkzeugkühlung an ihre Grenzen, sodass eine lokale konturnahe Kühlung des Gießwerkzeugs nur auf völlig neuem Weg, durch Implementierung eines neuartigen Werkzeugeinsatzes, zu realisieren ist. Dieser Werkzeugeinsatz enthält querschnittsoptimierte Kanalsysteme nahe der Werkzeugoberfläche und wurde als generativ gefertigtes Hybridbauteil durch Laserstrahlschmelzen hergestellt. Über einen separaten Temperierkreislauf wird eine besonders effektive Kühlung des Werkzeugeinsatzes realisiert.
Durch die Anwendung der konturnahen Kühlung wird der wesentliche Ausschussfaktor, der Porositätsanteil, im Bereich Ölfiltertopf deutlich reduziert. Dadurch werden die Herstellkosten gesenkt und die Zykluszeit minimiert. Der am Fraunhofer IWU entwickelte laserstrahlgeschmolzene Werkzeugeinsatz ist nachweislich praxistauglich und offeriert weiteres Potenzial in der Druckgusstechnologie der Zukunft.
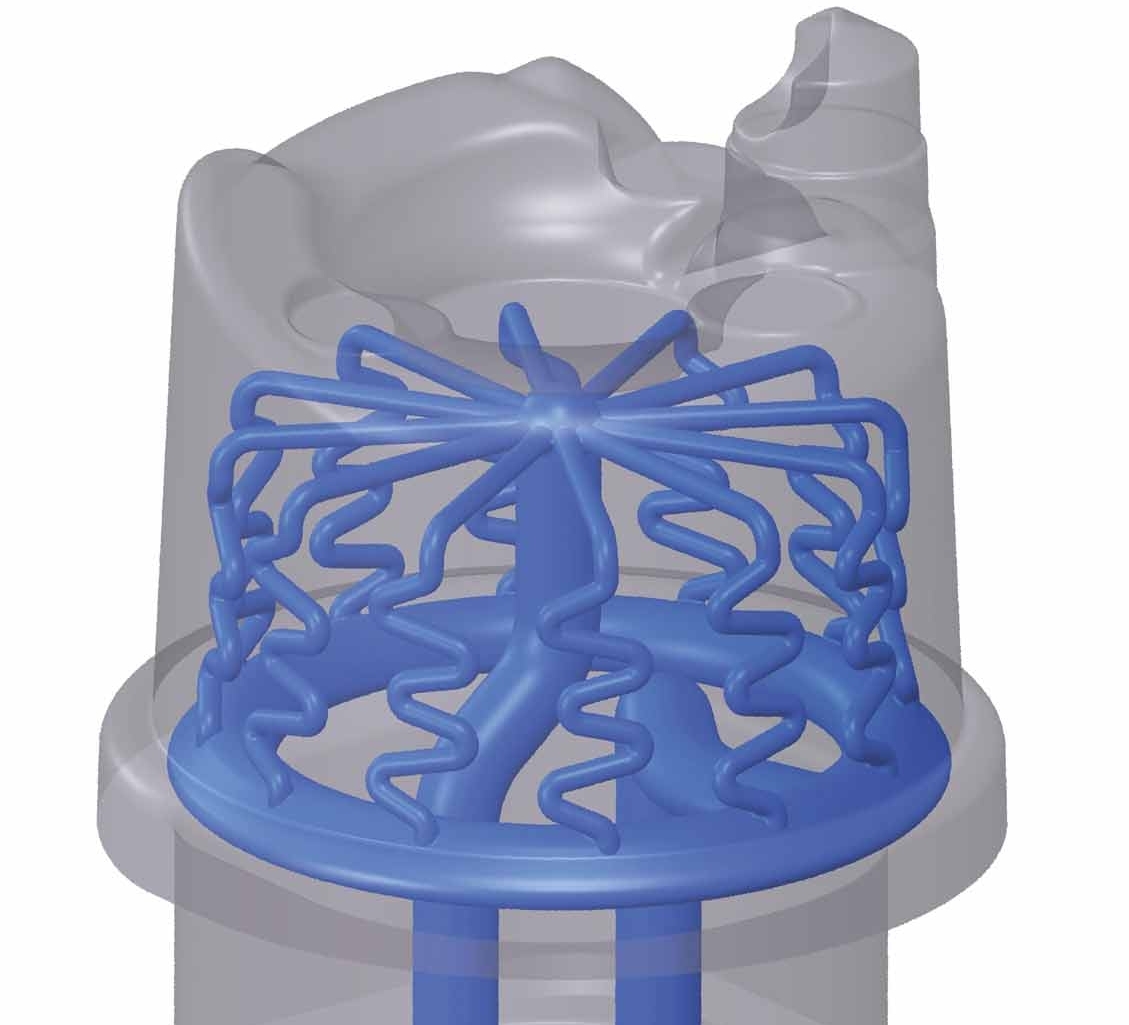